Электродуговой нагрев
4.1 Характеристика электрической дуги
4.2 Зажигание, устойчивость горения и регулирование тока дуги
4.3 Режимы сварки и работы источников питания сварочной дуги
4.4 Специальные виды дуговой сварки
4.4.1 Аргонодуговая сварка
4.4.2 Дуговая сварка в углекислом газе
4.4.3 Электрошлаковая сварка
4.4.4 Электронно-лучевая сварка
4.4.5 Плазменная сварка
4.5 Контактная сварка
4.6 Стыковая сварка
Контрольные вопросы
Лабораторная работа 6
Лабораторная работа 7
Электродуговой нагрев
4.1 Характеристика электрической дуги
Электрическая дуга (дуговой разряд), представляющая собой самостоятельный электрический разряд в смеси газов или паров металла между электродами, находящимися под напряжением, характеризуется малым анодно-катодным падением напряжения (10...20 В) и высокой плотностью тока (100...1000 А/см2). Электрический ток, протекающий в дуге, являющейся своеобразным проводником, в соответствии с законом Ленца - Джоуля преобразуется в теплоту, которую в условиях сельского хозяйства используют главным образом для расплавления металлов при сварке, резке и наплавлении.
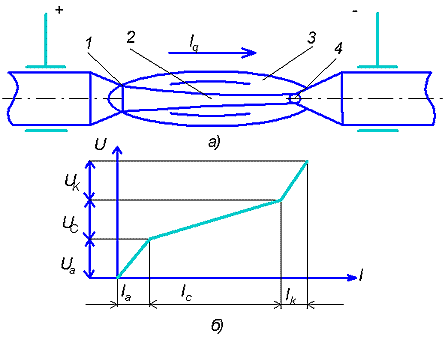 |
Рис. 4.1 Электрическая дуга (а) постоянного тока и распределение напряжения (б) на ее элементах: 1-анодный кратер; 2 - столб дуги; 3- светящаяся оболочка; 4 - катодное пятно. |
Известно, что в обычных условиях газы не проводят электрический ток, т. е. являются диэлектриками. Поэтому для горения электрической дуги необходимо наличие в газовом промежутке заряженных частиц - электронов или ионов. Электроны, развивая огромные скорости в дуге, сталкиваются с атомами и молекулами газа, превращают их в ионы и тем самым увеличивают его проводимость. Процесс образования электрически заряженных частиц в межэлектродном пространстве называют ионизацией. В электрической дуге ионизацию относят к типу самостоятельных разрядов, так как она происходит за счет энергии источника тока. В пространстве, где происходит разряд, выделяют катодную область 4 (катодное пятно) (рис. 4.0 а), столб 2 дуги, анодную область 1 (анодный кратер). Боковой поверхностью разрядного промежутка являются раскаленные газы 3 (светящаяся оболочка), не принимающие участия в прохождении тока. Материал электрода переносится от анода к катоду, поэтому на поверхности анода появляется углубление, а на поверхности катода - выступ, представляющий собой яркий светящийся участок.
На катоде происходит эмиссия электронов, дающая начало электрической дуге. Эмиссия электронов с поверхности катода может осуществляться за счет его нагревания (термоэлектронная эмиссия), а также за счет высокой напряженности (106 В/см) электрического поля в катодной области (автоэлектронная эмиссия). Плотность тока в катодном пятне очень высокая. В зависимости от материала электродов она составляет 1500...7000 А/см2, в анодном же кратере, имеющем по сравнению с катодным пятном большую поверхность, плотность тока снижается примерно в 10 раз.
Столб дуги, представляющий собой ярко светящуюся смесь электронов, положительных ионов и возбужденных нейтральных атомов, называемую плазмой, имеет температуру до нескольких тысяч градусов. Он непрерывно теряет заряженные частицы вследствие их рекомбинации, приводящей к образованию нейтральных атомов, и диффузии в окружающую среду. При стационарном процессе убыль заряженных частиц компенсируется ионизацией в столбе дуги.
Напряжение на дуге складывается из падений напряжений на отдельных ее областях - приэлектродных и столбе дуги. Длина катодной области порядка 10-5 см, а падение напряжения Uк на ней составляет 10...20 В, что объясняет высокую напряженность в данной зоне (рис.4.1 б). Напряженность электрического поля практически постоянна по всей длине столба дуги, а падение напряжения в нем зависит от протяженности участка. Длина анодной области 10-4 см, анодное падение напряжения Uа и напряженность электрического поля несколько меньше, чем в катодной области.
Напряжение на дуге и проводимость столба дуги зависят от значения тока. Эту зависимость при медленном изменении тока называют статической вольт-амперной характеристикой (ВАХ) дуги. ВАХ дуги при постоянных ее длине и диаметре электродов показана на рисунке 4.2.
Характеристика состоит из трех участков токов: малых I, средних II и больших III. На первом участке увеличение тока приводит к снижению напряжения дуги, так как при этом возрастают площадь поперечного сечения столба дуги и интенсификация процессов ионизации. Это способствует росту электропроводности канала дугового разряда.
На втором участке наступает равновесие процессов ионизации и деионизации в разрядном промежутке, площадь поперечного сечения столба дуги увеличивается и напряжение ее стабилизируется, т.е. становится независящим от значения тока. На третьем участке увеличение тока приводит к росту напряжения на дуге, так как катодное пятно занимает всю площадь торцов электродов, а сопротивление канала разряда стабилизируется.
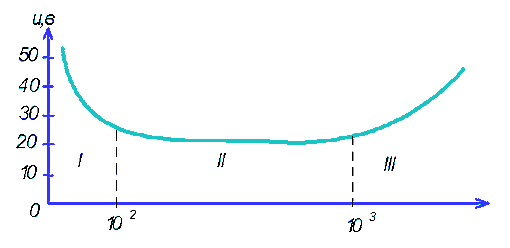 |
Рис. 4.2 Статическая вольт-амперная характеристика дуги постоянного тока |
Связь общего падения напряжения UД на дуге с падением напряжения на отдельных ее элементах в области малых токов устанавливает формула Г. Айртон:
где α - суммарное анодно-катодное падение напряжения, В; β- градиент потенциала в столбе дуги, В/м; l - длина дуги, м; γ и δ - мощности, затрачиваемые на вырывание электродов из катодного пятна, Вт/А, и на продвижение электронов в межэлектродном промежутке на единицу расстояния, Вт/(А.м); Iд - сила тока дуги, А.
В формуле (4.1) падение напряжения зависит от силы тока, что соответствует падающему характеру ВАХ. Для средних токов это слагаемое мало:
Среда, в которой дуга горит, влияет на форму статической ВАХ. Так, в среде инертных газов даже при небольших токах характеристика дуги возрастающая. Ее применяют при сварке в среде защитных газов, плазменно-дуговых процессах.
Рассмотренные явления происходят в электрической дуге постоянного и переменного тока. Статическая ВАХ на переменном токе соответствует действующим значениям тока и напряжения. При этом катодная и анодная области дуги меняются местами в зависимости от полярности приложенного напряжения. На рисунке 4.3 а, показано изменение тока и напряжения при отсутствии индуктивности в цепи дуги. При напряжении uист источника питания меньше напряжения Uз зажигания дуги она не может загореться. В обычной атмосфере напряжение Uз для стальных электродов составляет 30...35 В, а для угольных - 45...55 В. Через промежуток времени t1 напряжение источника увеличивается до Uз дуга зажигается и по ней протекает ток iД. достигнув амплитудного значения Uт, напряжение источника уменьшается и становится через промежуток времени t2 меньше напряжения UП погасания дуги, она гаснет, и ток через нее прекращается. На отрезке времени t3 +t1 дуга не горит, а затем происходят повторное ее зажигание, горение и погасание в отрицательной полуволне питающего напряжения.
Для маломощных дуг напряжение UП погасания несколько меньше напряжения Uз зажигания. При силе тока дуги более 100 А напряжение UП мало отличается от Uз и напряжение Uд горения практически не зависит от тока дуги, т.е. Uз ~ UП= Uд (рис. 4.3).
При включении индуктивности последовательно с дугой сдвигается ток относительно напряжения на угол φ (рис. 4.3, в). Изменяя значение индуктивности, можно получить такой угол сдвига фаз, что при уменьшении напряжения источника ниже напряжения горения дуги ЭДС самоиндукции, складывающаяся с напряжением источника, обеспечит напряжение, достаточное для поддержания горения дуги до тех пор, пока ток не перейдет через нулевое значение. В этот момент напряжение источника будет иметь другой знак и увеличится до значения, достаточного для зажигания дуги, т.е. ток в дуге возникает без всякого перерыва. При малом значении индуктивности появляются перерывы в горении дуги и кривая тока существенно искажается.
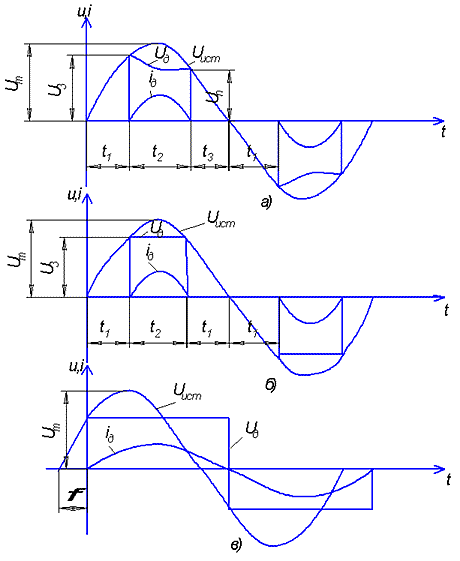 |
Рис. 4.3. Изменение тока iд и напряжения Uд в контуре с активным сопротивлением маломощных (а) и мощных (б) дуг, в контуре дуги с индуктивным (в) сопротивлением |
4.2 Зажигание, устойчивость горения и регулирование тока дуги
Источник питания сварочной дуги должен обеспечивать надежное зажигание дуги, ее устойчивое горение и регулирование тока.
Первоначально дуга зажигается при соприкосновении электродов, одним из которых является изделие, и при последующем их разведении. При соприкосновении электродов замыкается цепь источника питания, ток которого расплавляет и испаряет металл в месте контакта. При последующем отрыве электрода от изделия в пространстве, заполненном ионизированными газами и парами металла, под действием Напряжения источника возникает электрическая дуга. Она зажигается легче при высоком напряжении источника. Чтобы обеспечить надежное зажигание, напряжение холостого хода источника питания должно быть больше напряжения зажигания дуги. В то же время напряжение холостого хода должно быть безопасным для сварщика.
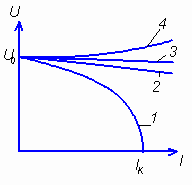 |
Рис. 4.4. Внешние характеристики источников питания сварочной дуги: 1 и 2 - круто- и пологопадающая; 3 - жесткая; 4-возрастающая. |
Основная характеристика источника - внешняя, представляющая собой зависимость между напряжением на клемах и током, протекающим через сварочную цепь при нагрузке. Внешняя вольт - амперная характеристика (рис. 6.4) может быть крутопадающей 1, пологопадающей 2, жесткой 3 и возрастающей 4. Важным параметром источника наряду с напряжением Uо холостого хода является ток Iк короткого замыкания, который по отношению к номинальному току Iн источника обычно находится в следующих пределах:
Таким образом, короткое замыкание - один из рабочих режимов при зажигании электрической дуги. Источник питания при этом должен надежно работать.
Устойчивое горение дуги обеспечивается правильным выбором внешней характеристики источника питания (рис. 6.5). При падающей статической ВАХ 2 дуги источник питания должен иметь еще более крутопадающую внешнюю характеристику 1. Равенство токов и напряжений дуги и источника в этом случае будет в точках А и В. Из них только точка А соответствует устойчивому горению дуги.
В статическом состоянии баланс напряжений в сварочной цепи имеет вид
Uо - напряжение холостого хода источника питания, В; Iд - сила тока сварочной цепи, А; Rи - сопротивление источника питания, Ом; Uд - напряжение дуги, В.
При изменении тока в сварочной цепи баланс мгновенных напряжений выглядит следующим образом:
где L - индуктивность контура сварочной цепи, Гн; di/dt - изменение мгновенного значения сварочного тока, А/с,
ЭДС самоиндукции контура с дугой
В точке В при увеличении тока I1 на ΔIYL(di/dt)>0. Так как L>0, то di/dt >0, то в результате ток в цепи будет продолжать расти до значения Iа. При уменьшении тока и ΔIYL(di/dt)<0 и di/dt<0, вследствие чего ток будет уменьшаться до нуля и дуга погаснет. Следовательно, режим в точке В неустойчивый.
Иначе обстоит дело в точке А. Если ток I2 возрастет на ΔI то в соответствии с уравнением (4.6) L(di/dt)<0 и di/dt<0. В результате ток будет уменьшаться до значения I2. При снижении тока I2 на ΔIYL(di/dt)>0 и di/dt>0, вследствие чего ток возрастает до прежнего значения I2, т.е. дуга горит устойчиво.
При жесткой статической ВАХ устойчивое горение дуги обеспечивается при использовании источников питания с круто- и пологопадающей внешней характеристикой. При возрастающей статической ВАХ дуги применяют источники с жесткими внешними характеристиками.
Сварочный ток при питании дуги от источника с падающей ВАХ можно регулировать, изменяя полное сопротивление цепи дуги, ее длину, напряжение холостого хода источника питания.
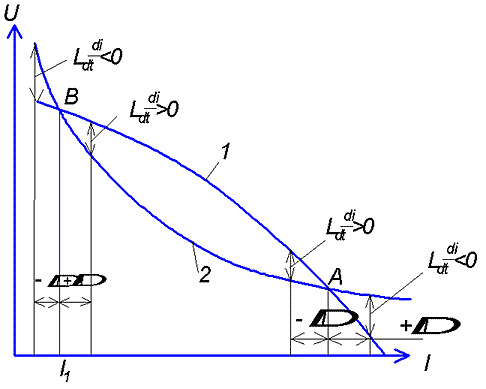 |
Рис. 4.5. Внешняя характеристика 1 - источника питания и вольт-амперная 2- дуга. |
При изменении полного сопротивления цепи дуги (рис. 4.6) можно уменьшать сварочный ток от номинального значения до значения, соответствующего пересечению статической ВАХ дуги и внешней характеристики источника. При большом полном сопротивлении цепи дуга вообще гореть не будет, так как для любого значения тока напряжение питания будет меньше напряжения, необходимого для горения дуги.
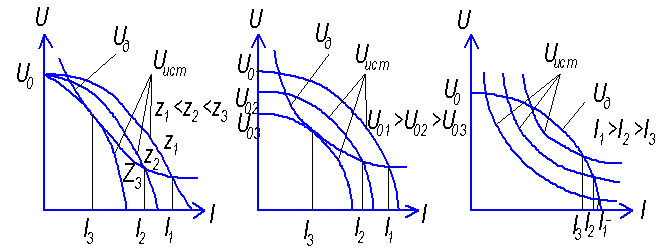 |
Рис. 4.6. Регулирование тока (а) изменением полного сопротивления цепи дуги, напряжения (б) холостого хода, длины (в) дуги |
При уменьшении напряжения холостого хода источника его внешние характеристики смещаются влево (рис. 4.6, б) и пересекаются со статической ВАХ дуги при меньших значениях тока. Очевидно, что снижать напряжение холостого хода источника можно до значений, при которых обеспечивается зажигание дуги. При увеличении ее длины статические ВАХ смещаются вверх, а точки их пересечения с внешней характеристикой источника будут соответствовать меньшим значениям тока (рис. 4.6, в). При черезмерном увеличении длины дуга погаснет.
Кроме основных требований по обеспечению надежного зажигания, устойчивости горения и регулирования сварочного тока, которые являются общими для всех источников питания сварочной дуги, к источникам переменного тока предъявляются дополнительные требования. Они связаны с их динамическими свойствами, т. е. способностью восстанавливать напряжение в соответствии с изменившимся током. Так, при погасании дуги напряжение должно быстро восстанавливаться до значения зажигания, так как в противном случае повторного зажигания может не произойти и в горении дуги наступят значительные перерывы. Для надежного повторного зажигания дуги переменного тока необходимо увеличивать сварочный ток и напряжение холостого хода источника, а также использовать источники с большой индуктивностью.
От динамических свойств источников переменного тока зависит качество сварочного шва. Быстрое нарастание тока короткого замыкания при касании каплей электродного металла шва приводит к ее разбрызгиванию и ухудшению качества сварочных работ. Для устранения этого в сварочную цепь последовательно с дугой включают дроссель или применяют источники с крутопадающими характеристиками.
4.3 Режимы сварки и работы источников питания сварочной дуги
Швы сварных соединений в зависимости от взаимного расположения деталей подразделяют на стыковые, угловые, тавровые и нахлесточные форма и размеры шва зависят от режима сварки. При ручной дуговой сварке основными параметрами режима являются диаметр электрода, значения тока и напряжения, род и полярность тока скорость сварки.
Для высокой производительности сварочного процесса и получения качественного соединения дуга должна гореть устойчиво. Это зависит от многих факторов, среди которых основное значение имеют характеристики источников питания и наличие в материале свариваемых деталей и электродов - элементов с малым потенциалом ионизации. Для повышения устойчивости горения дуги переменного тока во флюсы вводят элементы с низким потенциалом ионизации - калий, кальций, натрий. Однако ее же на постоянном токе дуга горит надежнее. Поэтому качество сварного шва, выполненного на постоянном токе, выше, чем на переменном.
При выборе значения сварочного тока необходимо помнить, что с его увеличением возрастает количество выделенной теплоты и повышается давление дуги. При этом глубина провара возрастает. Большой ток повышает скорость плавления электрода и приводит к образованию швов с повышенной напряженностью металла.
Значение сварочного тока определяется также видом соединения: тавровые и нахлесточные соединения выполняют большим током по сравнению со стыковым.
Если для работ используют электроды диаметром 1,5...6 мм, что соответствует толщине свариваемого металла 0,5...10 мм, значение рабочего тока ориентировочно можно определить по формуле
где К - коэффициент, зависящий от диаметра электрода и вида покрытия, А/мм;
dэл - диаметр электрода, мм. При этом руководствуются следующими данными:
Таблица 4.1
dэл, мм | 1…2 | 3…4 | 5…6 |
К, А/мм | 25…30 | 30…45 | 45…60 |
Большие значения коэффициента К принимают при выполнении горизонтальных сварных швов. Для получения вертикальных швов сварочный ток уменьшают на 10.. 15 %, а потолочных - на 15 ... 20 %.
С уменьшением диаметра электрода при неизменной силе тока возрастает плотность тока. стабилизируется перемещение.
4.4 Специальные виды дуговой сварки
4.4.1 Аргонодуговая сварка
Сущность данного метода сварки заключается в том, что дуга горит между концом электрода и свариваемым изделием в среде защитного инертного газа - аргона. Помимо защиты от вредного воздействия окружающей среды аргон выполняет несколько положительных функций:
- способствует улучшению устойчивости горения дуги из-за меньшего катодного падения напряжения, чем в воздухе;
- из-за меньшей теплопроводности аргона уменьшаются тепловые потери столба дуги, что также приводит к увеличению устойчивости горения дуги;
- при разряде в аргоне происходит катодное распыление металла, что приводит к его очистке, в частности от оксидов, например от оксида алюминия и улучшению качества шва.
Технические данные аппаратов для аргонодуговой сварки приведены в таблице 4.2. При горении дуги возникает термоэмиссия с катода.
Таблица 4.2
Тип аппарата | Основное назначение | Толщина детали, мм | Род тока | Номин ток, А | Диаметр электрода, мм |
УДАР-300 | Сварка алюминиевых сплавов | 1-12 | ~ | 300 | 2-6 |
УДАР-500 | Сварка нержавеющей стали | 1,5-20 | ~ | 500 | 2-10 |
АГВ-2 | Автоматическая сварка различных металлов | 0,8-16 | = | 400 | 2-6 |
АВТ | Автоматическая сварка труб из нержавеющей стали | 0,5-10 | = | 250 | 1-3 |
Это явление нежелательное, поэтому для увеличения тепловой мощности дуги применяют обратную полярность. Кроме того, при прямой полярности расплавленная ванна металла покрывается пленкой окиси, что препятствует сплавлению деталей. Поэтому аргонодуговую сварку ведут на переменном токе или на постоянном токе обратной полярности. При сварке на переменном токе в схему включается осциллятор для облегчения зажигания дуги и для повышения устойчивости ее горения.
Аргонодуговая сварка производится с плавящимся и неплавящимся вольфрамовым электродом. Чаще используется неплавящийся вольфрамовый электрод. При работе на постоянном токе применяются обычные сварочные генераторы с баластными реостатами РБ-200, РБ-300, включаемыми последовательно в сварочную цепь для регулирования сварочного тока при малых значениях и для обеспечения устойчивости горения дуги. Максимальный сварочный ток некоторых горелок составляет А) ГРАД-200-250, ГРАД-400-400, ЭЗР-3-58-100, АР-10 малая-120, АР-10 большая-400. Напряжение холостого хода 130-200В.
4.4.2 Дуговая сварка в углекислом газе
Сущность этого метода заключается в том, что в зону сварки с постоянной скоростью подается электродная проволока диаметром 0,5-2 мм в струе углекислого газа (рис. 4.7). Роль углекислого газа состоит в защите расплавленного металла от окружающей среды. С целью уменьшения окисляющего действия углекислого газа электродная проволока имеет повышенное содержание раскисляющих элементов (марганца, кремния).
Данный способ сварки особенно эффективен для сварки металлов небольших толщин порядка 1-2 мм и особенно для швов сложной конфигурации, так как их сварка другими способами, например под флюсом, затруднена или вообще невозможна закрытия шва слоем флюса.
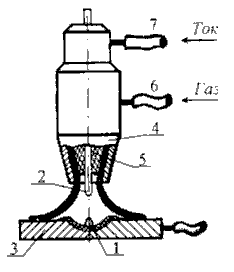 |
Рис. 4.7 Схема сварки в углекислом газе. 1 - расплавленный металл, 2-электрод, 3-свариваемые детали, 4- горелка, 5- керамическая насадка, 6- штуцер для подачи газа, 7- токоввод |
Сварка в углекислом газе выполняется в полуавтоматическом ил" автоматическом режиме. Для этого используются источники постоянного тока:
- преобразователи ПСО - 300, ПС-500, ПСМ - 1000 и др,
- выпрямители ВС - 200, ВС - 300, ВС - 500,
- генераторы типа ГРС.
Горелки для полуавтоматической сварки бывают двух типов:
- для сварки на малых токах без водяного охлаждения (до 300 А).
- для сварки на больших токах с водяным охлаждением. Для сварки используется углекислый газ, получаемый из углекислоты, транспортируемой в черных баллонах с желтой надписью "СО2 сварочный" емкостью 40 л, в который заливается 12,7 м3 углекислоты, дающей при испарении 25 кг углекислого газа. Если использовать пищевую углекислоту, то ее необходимо осушать, для этого между баллоном и редуктором устанавливается осушитель газа.
Наилучшие результаты получаются при сварке различных видов сталей и особенно при работе на постоянном токе обратной полярности. В этом случае уменьшается разбрызгивание металла, уменьшается устойчивость горения дуги.
4.4.3 Электрошлаковая сварка
Принцип данного вида сварки заключается в том, что расплавление электродного металла и свариваемых деталей осуществляется за счет протекания электрического тока через расплавленный флюс (шлак), обладающий электропроводностью. Этот вид обеспечивает сварку деталей большой толщины, доходящей до 2.5м, что невозможно осуществить другими способами сварки.
Свариваемые детали заключаются в медные водоохлаждаемые ползуны и нижнюю (начальную)и верхнюю(конечную) планки, служащие одновременно для начала и окончания шва. Шлаковая ванна формируется внизу, в колодце, образованном свариваемыми деталями, держателями и нижней планкой. По мере сваривания деталей медные держатели поднимаются вверх со скоростью, равной скорости образования шва.
Шлаковая ванна образуется или прямым пропусканием тока через шлак и предварительным нагревом шлака в отдельной установке и последующим заливом его в колодец. При этом обеспечивается устойчивое горение дуги. На устойчивость горения дуги влияет также внешняя характеристика источника, которая должна быть жесткой или несколько возрастающей - с увеличением тока в ванной напряжение должно быть или неизменным, или возрастать.
Электроды могут быть проволочными, пластинчатыми или ленточными. Может быть один или несколько электродов. Наиболее распространенные аппараты с одним и тремя электродами, хотя могут быть (и имеются) аппараты с 9 и 18 электродами. Данные некоторых аппаратов электрошлаковой сварки приведены в таблице 10-3.
4.4.4 Электронно-лучевая сварка
Принцип электронно-лучевой сварки заключается в концентрированном нагреве соединяемых деталей за счет использования кинетической энергии ускоренных электронов в высоком вакууме. В результате бомбардировки электронным пучком кинетическая энергия превращается в теплоту, используемую для осуществления сварки плавлением.
Для осуществления этого вида сварки необходимо получить свободные электроны, сфокусировать их в тонкий пучок и ускорить до необходимой энергии. Все это осуществляется в устройстве, называемом электронной пушкой. Свободные электроны получаются из накаленного катода, а ускорение осуществляется при прохождении электронами электрического поля высокой напряженности между катодом и анодом. Фокусировка пучка осуществляется специальной магнитной линзой, а его отклонение в заданном направлении или сканирование по определенной программе осуществляется отклоняющими катушками.
Таблица 4.3
Технические характеристики аппаратов электрошлаковой сварки
Тип аппарата | Толщина деталей, мм | Номин. ток | Uраб, В | Кол-во элек-в | Диаметр электрода |
А-306А: Сварка прямолинейных | 20-60 | 800 | 40 | 1 | 3-5 |
А-372Р: Сварка прямолинейных и | До 450 | 300 | 45-55 | 3 | 3 |
А-741: Сварка прямолинейных и переменной кривизны стыков | До 2500 | 9000 | 36-55 | 3 | 3 |
Этот способ сварки имеет ряд существенных достоинств перед другими, главными из которых являются следующие:
1. Плотность поступающей в зону энергии можно очень точно регулировать, что позволяет широко варьировать глубину провара толщину свариваемых изделий.
2. Возможна сварка деталей любой конфигурации, поскольку электронный луч легко управляется с помощью электрических и магнитных полей, то возможна сварка деталей любой конфигурации.
3. Околошовная зона имеет очень незначительную толщ] поэтому при сварке практически не происходит нагрев свариваемых деталей.
4. Возможность фокусировки пучка электронов до микрон) размеров позволяет использовать этот вид сварки для целей микроэлектроники, радиотехники.
5. Сварка в вакууме исключает любое окисление свариваемых. деталей. Это позволяет соединять детали из весьма тугоплавких материалов, таких как молибден, вольфрам, что недоступно для других способов сварки.
Недостатком данного способа является наличие вакуумных насосов и вакуумных систем, а также сложность устройства и технологии, ] требует высококвалифицированного обслуживающего персонала.
Параметры некоторых типов установок для электронно-лучевой сварки приведены в таблице 44.
Таблица 4.4
Тип установки | Диаметр камеры | Длина камеры | Uкв, В | I, мА |
ЭЛУ4 Общие виды сварки | 700 | 1200 | 60 | 35 |
У-74: Сварка труб | 800 | 1000 | 40 | 75 |
У-101 Сварка труб | 500 | 500 | 25 | 500 |
Конструкционной основой электронно-лучевой сварки являете вакуумная камера на которой сверху монтируется электронная пушка.
Камера имеет герметические вводы дли подачи энергии, подачи охлаждающей воды, передачи движения к находящимся внутри механизма перемещения свариваемых деталей. Камера откачивается форвакуумными и высоковакуумными насосами для создания разряжения не выше 10-3 Па.
Ток пучка, а значит и мощность нагрева можно регулировать как изменением тока накала катода и плотности тока ускоренных электронов, а также ускоряющим напряжением. Катоды пушек могут быть прямонакаленные вольфрамовые в виде спиралей или нитей или подогревные, состоящие из подогревного катода и подогревной таблетки. Подогревные катоды обычно изготавливаются из гексаборида лантана, дают значительно большую плотность тока, чем прямонакальные. Но они более сложны в изготовлении.
4.4.5 Плазменная сварка
Плазменная сварка и плазменная резка основаны на создании плазменного столба или плазменной струи - потока высокоионизированных частиц с большим запасом энергии, позволяющим достигать температуры 20000К.
Для создания потока ионизированных частиц используется дуговой разряд между двумя электродами в продуваемом инертными газами канале, стенки которого охлаждаются водой. За счет охлаждения внешней части плазменного столба, он концентрируется в центре канала, что приводит к высокой степени ионизации газа и концентрации в нем большой энергии. Эта энергия и используется для сварки или резки металлов.
Источниками питания плазменного сварочного аппарата являются сварочные генераторы постоянного тока или сварочные выпрямители. Возбуждение дугового разряда осуществляется осциллятором, включаемым параллельно источнику тока, а регулирование сварочного тока осуществляется балластным сопротивлением, включаемым последовательно источнику тока.
Мощность плазменной горелки существенно зависит от состава газа. Например, смесь 86% гелия и 14% аргона дает мощность в 2 раза большую, чем при использовании чистого аргона, что объясняется более высоким потенциалом ионизации гелия. Длина яркосветящегося ядра плазменной струи может меняться от 2 -3 до 40 -50 мм в зависимости от геометрии канала, состава и скорости подачи газа, тока и напряжения дуги.
Плазменная струя нашла наиболее широкое применение для резки металлов, не поддающихся обычным способам резки, например, для резки нержавеющей стали, меди, алюминия, керамики. Обычно используется смесь аргона с водородом, концентрация которого может достигать 30%. Плазменной струей можно сваривать металлы и неметаллы, а также их сочетания. В таблице 4.5 приведены параметры установок плазменной сварки.
Таблица 4.5
Тип установки | Назначение | Uхх,В | Номин. ток, А | Wпотр, кВт |
УПСР-300-2 | Сварка нерж.стали до 5мм | 65 | 300 | 16 |
А-1255 | Сварка мет. и сплавов до 1мм | 55 | 10 | 0,8 |
А-1326 | Сварка мет. и сплавов до 1мм | 80 | 30 | 2,5 |
4.5 Контактная сварка
Контактная сварка или сварка сопротивлением.
Этот вид сварки относится к одной из разновидностей сварки давлением, при которой детали механически сжимаются для получения соединения и в месте стыка каким-то образом подводится энергия, используемая для разогрева свариваемых деталей. При контактной сварке или сварке сопротивлением энергия выделяется за счет пропускания тока через свариваемые детали и выделения тепловой энергии на большом сопротивлении контакта. Если сами детали не являются практически сопротивлением электрическому току, то место стыка представляет большое сопротивление и вся выделяемая на нем тепловая энергия идет на разогрев деталей.
Контактная сварка бывает трех разновидностей, определяемых геометрией шва и электродов: стыковая, точечная, роликовая. На рис. 10-6 показаны эти типы сварки. Во всех случаях переходное сопротивление контакта может быть определено выражением
где К1 - коэффициент, зависящий от материала контакта деталей;
Fk - усилие сжатия контакта; m- коэффициент, учитывающий форму поверхностей контактирующих деталей; Кt- коэффициент, учитывающий температуру контакта.
где α - температурный коэффициент сопротивления материала,
Т - температура контакта.
При Т близкой к комнатной Кт можно принять равным единице.
Значение коэффициента К1, для различных пар свариваемых деталей следующее:
АL-АL-0,006; Сu-Сu-0,0004; АL-Сu-0,001 сталь-сталь-0,0076; Аg-Аg-0,0006; латунь-латунь-0,00067
Значение m для контакта плоскость - плоскость равно единице, для контактов сфера - сфера и сфера - плоскость m=0,5.
Из этих численных значений коэффициентов следует, что чем лучше контакт, тем больше m, меньше К1 и тем меньше сопротивление.
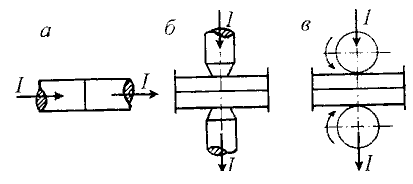 |
Рис. 4.8. Основные разновидности контактной сварки: а - стыковая, б - точечная, в - роликовая. I - направление сварочного тока |
4.6 Стыковая сварка
При стыковой сварке торцы свариваемых деталей приводятся в соприкосновение, после чего через них пропускается ток, место стыка разогревается до необходимой температуры и продольным сжатием достигается сплошность соединений - осуществляется пластическая сварка. По окончанию цикла сварки ток выключают и снимают усилие.
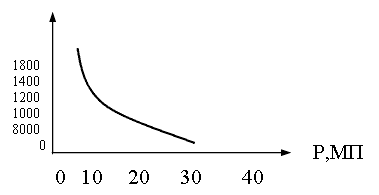 |
Рис. 4.9 Зависимость усилия сжатия от температуры разогрева при стыковой сварке малоуглеродистой стали |
При стыковой сварке два параметра взаимосвязаны друг с другом -температура стыка и сжимающие усилие. Чем выше температура, тем меньше требуется усилие. На рис. 4.9 такая зависимость приведена для малоуглеродистой стали.
Стыковая сварка бывает двух видов: без оплавления (сварка сопротивлением) и с оплавлением. В первом случае нагрев торцов осуществляют только пропусканием тока. Токи очень большие, достигают 5-10кА, удельная мощность составляет 10-15 кВт/см2. Соединяемые детали в этом случае, как правило, небольшого поперечного сечения. Во втором случае сварка производится в несколько стадий: предварительный подогрев, оплавление и окончательная осадка. Вначале усилие составляет 5-20 МПа, затем включается ток и происходит разогрев места стыка до 900-1100 К, после этого сжимающие усилие снижают до 2-5 МПа, что приводит к увеличению сопротивления контакта и снижению тока. В это время контакт осуществляется на небольшой площади, на выступающих остриях, где температура повышается до температуры плавления и выступы исчезают. Затем такой же процесс происходит на следующих выступах и т. д. Очередные выступы разогреваются также за счет теплопроводности. Происходит перегрев металла на выступах, его парообразование, выбрасывание пара и частиц жидкого металла из зоны стыка. Часть жидкого металла стекает вниз.
Контрольные вопросы
1. Как формируются падающие характеристики в сварочном трансформаторе?
2. Перечислите способы регулирования сварочного тока.
3. Какие величины определяют из опытов холостого хода и короткого замыкания?
4. Назовите способы сварки сварочными трансформаторами.
5. Как осуществляется плавное регулирование сварочного тока?
6. Каким должно быть безопасное напряжение для работы сварщика?
7. Для каких целей при сварке необходимо регулирование сварочного тока?
|