Учебник Михайлова
Глава вторая. Технологические операции, выполненные электровзрывным способом
2.1. Схемы выпрямителей для электровзрывной обработки
2.2. Физические процессы при электроимпульсном разрушении материалов
2.3. Бурение скважин
2.4. Разрушение бетона и железобетона
2.5. Дробление руд
2.6. Штамповка, выдавливание и вытяжка деталей
2.7. Раздача труб
2.8 Электроимпульсное дробление глубокоохлажденных резин и резинотехнических изделии, армированных металлом
ЧАСТЬ IX. МАГНИТНО-ИМПУЛЬСНЫЕ ТЕХНОЛОГИИ
Глава первая. Физические основы магнитно-импульсных технологии
1.1. Физика процессов в токопроводящих материалах под действием импульсного магнитного поля
1.2. Принципиальная схема установки для магнитно-импульсной обработки
2.1. Особенности магнитно-импульсного формообразования
2.2. Инструмент для магнитно-импульсной обработки
2.3. Штамповка с помощью импульсных магнитных полей
2.4. Сборочные операции, выполняемые с использованием импульсного магнитного поля
ЧАСТЬ X. ЭЛЕКТРИЧЕСКАЯ СВАРКА
Глава первая. Дуговая электрическая сварка
1.1. История развития электрической сварки
1.2. Классификация электрической сварки
1.3. Дуговая электрическая сварка плавлением
Глава вторая. Специальные виды дуговой сварки
2.1. Аргонодуговая сварка
2.2. Дуговая сварка в углекислом газе
2.3. Электрошлаковая сварка
2.4. Электронно-лучевая сварка
2.5. Плазменная сварка
Глава третья. Контактная сварка
3.1. Контактная сварка или сварка сопротивлением
3.2. Стыковая сварка
Глава вторая. Технологические операции, выполненные электровзрывным способом
2.1. Схемы выпрямителей для электровзрывной обработки
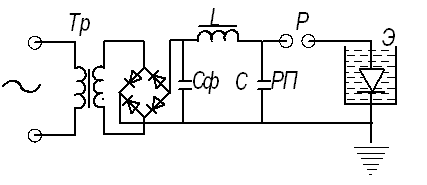 |
Рис. 8-2. Схема выпрямителя на постоянном токе |
Принцип работы выпрямителей, применяемых в электровзрывных технологиях заключается в заряде конденсатора высокого напряжения до необходимой величины и его разряде через разрядный промежуток и последовательно соединенный с ним формирующий промежуток (разрядник). Роль формирующего промежутка заключается в формировании импульса необходимых параметров - повышение крутизны фронтов и сокращение длительности.
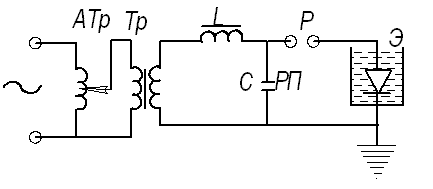 |
Рис. 8-3. Схема выпрямителя на переменном токе |
Разработано большое число выпрямителей, различающихся наличием дополнительных элементов: автотрансформатора, ограничивающего сопротивление и ёмкость в первичной цепи, фильтра, состоящего из конденсатора и индуктивности (дросселя). На рис. 8-2 и 8-3 приведены схемы выпрямителей на переменном и постоянном токе.
Здесь АТр - автотрансформатор, L - дроссель, Сф - конденсатор фильтра.
2.2. Физические процессы при электроимпульсном разрушении материалов
При разрушении материалов электроимпульсным способом используется зависимость прочности диэлектрической среды от длительности импульса. С уменьшением времени воздействие импульсного напряжения прочность жидких диэлектриков растет быстрее, чем твердых диэлектриков. Если при статическом напряжении (Цст) электрическая прочность твердых диэлектриков, как правило, превышает прочность жидких диэлектриков, то при импульсном напряжении (U имп) при длительности импульса менее 10 с электрическая прочность жидких диэлектриков возрастает так, что становится выше прочности твердых диэлектриков и горных пород.
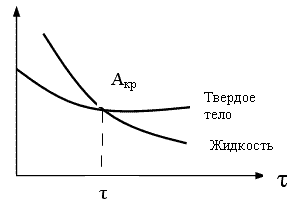 |
Рис. 8-4. Вольт-секундная характеристика твердого тела и жидкости |
При помещении материалов в жидкость, например в техническую воду, и при подаче на приложенные к материалу электроды импульса напряжения с очень крутым передним фронтом произойдет электрический пробой по объёму твердого тела между электродами и дальнейшее его разрушение. На рис. 8-4 показаны Вольт-секундные характеристики (зависимость пробивного напряжения Uпр от длительности импульса) твердого тела и жидкости. Из рисунка следует, что до критической точки (Акр) при длинных импульсах пробивное напряжение у твердого тела выше, чем у жидкости. При меньших значениях Uпр ситуация противоположная - электрическая прочность жидкости выше электрической прочности твердого тела. Поэтому при осуществлении технологических операций разрушения материалов длительность импульса должна быть меньше значения τкр для данной жидкости и твердого тела.
При разрушении различных материалов необходимо подбирать соответствующую жидкость. В реальных установках, как правило, используется вода, трансформаторное масло, дизельное топливо.
Электроимпульсный способ используют для бурения скважин, дробления материалов, разрушения железобетонных изделий. На рис. 8-5 показаны принципиальные схемы бурения скважин и разрушения железобетонных изделий электроимпульсным способом.
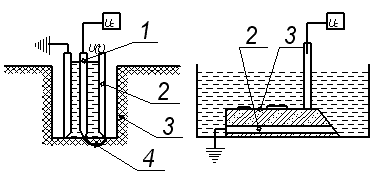 |
Рис.8-5 Принципиальная схема бурения скважин (а) и разрушения железобетонных изделий (б) электроимпульсным способом. 1-высоковольтный электрод, 2-заземлённый электрод, 3- разрушаемая порода, 4- искровой канал, UC;-источник высокого напряжения |
2.3. Бурение скважин
Бурение скважин электроимпульсным способом эффективно для прочных и особо прочных пород и для мёрзлых грунтов. Диаметр скважины должен быть не менее 100-150 мм, так как эффективность бурения увеличивается с увеличением диаметра, Эффективность по сравнению с механическим способом бурения возрастает для скважин некруглого сечения, при бурении в затрудненных для вращения условиях ( под водой, в условиях ограниченного пространства).
2.4. Разрушение бетона и железобетона
Разрушение бетона и железобетона является важной проблемой, поскольку при их производстве значительную долю составляет некондиционная часть продукции. Кроме того, источниками отходов являются сносимые здания и сооружения, автодорожные покрытия. Переработка указанных отходов позволяет вернуть металлическую арматуру и минеральное сырьё в производство и решить дополнительные проблемы (освобождение земельных угодий, очистку территорий и т. д.).
При механических способах разрушения себестоимость операций очень высокая за счет износа разрушающего инструмента, низкого КПД, трудностей концентрации достаточного количества энергии. Проблема усложняется тем, что необходимо полностью отделить бетон от арматуры.
Электроимпульсная технология является безотходной, т.к. позволяет полностью разделить бетон и арматуру, причем арматурный каркас может быть использован повторно.
2.5. Дробление руд
Дробление руд электроимпульсным способом позволяет получить фракции необходимого размера. Особенно благоприятными для данного способа являются геологические объекты и искусственные материалы, в которых электрические и физико-механические свойства полезного компонента и вмещающих руд сочетаются так, что полезный компонент обладает высокой электрической прочностью и пластичностью, а вмещающая порода обладает меньшей электрической прочностью и высокой хрупкостью.
При электрическом способе дробления таких пород, пробой осуществляется во вмещающей породе, которая, хрупко разрушаясь, измельчается, оставляя не поврежденными крупные кристаллы.
Особенность электроимпульсного способа дезинтегрировать компоненты руд по пробивному напряжению позволяет достигать высокой производительности данной технологии и реального ее применения на обогатительных фабриках.
2.6. Штамповка, выдавливание и вытяжка деталей
Данные операции позволяют получать из листов различных металлов и сплавов детали различной конфигурации и формы. Например, получать детали сферической или конической формы, получать гофры на трубчатой заготовке. В этой технологии используют давление ударной волны, образованной при подаче импульсного напряжения на электроды и возникновении разряда.
Схемы электровзрывного получения гофр на трубчатой заготовке и штамповки плоской заготовки показаны на рис. 8-6.
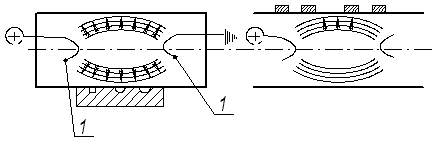 |
Рис. 8-6. |
2.7. Раздача труб
Для получения труб такой формы, чтобы на концах они имели сужение, через которое производилась бы их стыковка, используют безматричную раздачу тепловым взрывом.
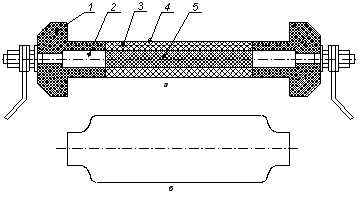 |
Рис. 8-7. |
Принцип работы такой технологии заключается в испарении помещенного внутрь трубы взрывного стержня при подаче на него импульса напряжения и образовании необходимого объёма газов. Образованные при взрыве газы разогревают и раздавливают полиэтиленовую втулку, вставленную в трубу, которая в свою очередь раздавливает трубу. Если труба на концах не имеет полиэтиленовой вставки и взрывного стержня и в концы вставлены упоры, например из текстолита, то они остаются без изменения и после обработки их диаметр становится меньше диаметра всей трубы. Схема раздачи труб показана на рис. 8-7.
2.8 Электроимпульсное дробление глубокоохлажденных резин и резинотехнических изделии, армированных металлом
Постоянное накопление резиновых и полимерных отходов требует эффективных методов их переработки с целью возврата в производство ценного сырья и улучшения экологического состояния территорий. В настоящее время наиболее перспективной является переработка отходов резиновой промышленности и резинотехнических изделий, включающая их предварительное измельчение. Для этого необходимы рациональные способы получения из них резиновой крошки различной степени дисперсности. В последние 10-15 лет для этого традиционно используется техника криогенного измельчения, реализующая разрушение материала, охлажденного до температуры хрупкости, на механических установках. Такая технология имеет два существенных недостатка при переработке резино-металических отходов:
1) значительный износ рабочих инструментов;
2) большая толщина металлических включений (более 2-3 мм)
При электроимпульсном дроблении рабочим инструментом являются электрические разряды, процесс разрушения можно регулировать величиной энергии и длительностью импульса, что позволяет получать крошку заданной дисперсности. Кроме того, при разрушении резинотехнических изделий, армированных металлом, возможно полное отделение резины от металла.
В таблице 8-1 приведены значения энергии импульса (\У), производительности импульса (а), условных энергозатрат (А) при дроблении резин марки ШБТМ и ТСШ электроимпульсным методом.
Оптимальная частота посылки импульсов составляет 6-8 имп/с, расход жидкого азота для охлаждения равен 0,005 лс/имп. Сравнение абсолютных значений удельных показателей энергетических характеристик разрушения горных пород и резинотехнических изделий показывает, что для горных пород они на порядок выше.
Таблица 8-1 Значения параметров дробления резин электроимпульсным методом
Марка резины | Размеры, мм | W, Дж | А, Г/имп. | А, кВтч/кг |
исходный | конечный |
ШБТМ | 30-50 | 2 | 550 | 1,01 | 0,1 |
1 | 630 | 0,63 | 0,16 |
ТСШ | 30-50 | 2 | 580 | 1.15 | 0.1 |
1 | 700 | 0.47 | 027 |
ЧАСТЬ IX. МАГНИТНО-ИМПУЛЬСНЫЕ ТЕХНОЛОГИИ
Глава первая. Физические основы магнитно-импульсных технологии
1.1. Физика процессов в токопроводящих материалах под действием импульсного магнитного поля
При взаимодействии импульсного электро-магнитного поля с током, индуцированным этим полем в токопроводящих материалах осуществляется их деформация. Между индуцированным током и электромагнитным полем возникает взаимодействие, которое создает значительные силы давления, деформирующие токопроводящий материал-заготовку. Величина давления определяется индукцией поля.
Деформацию осуществляют двумя путями:
1) электродинамическим при взаимодействии токов в возбудителе и заготовке, включенной в цепь разряда конденсатора, создающего магнитное поле;
2) индукционным при взаимодействии импульсного магнитного поля с наведенными этим же полем в заготовке токами; при этом заготовка не включена в электрическую цепь, создающую поле.
Индукционный способ. Этот способ получил более широкое распространение, так как заготовка в этом случае не включена в электрическую цепь, что упрощает схему.
Электродинамический способ основан на законе электротехники о взаимодействии двух параллельных проводников, по которым протекает ток. Сила взаимодействия, возникающая между проводниками пропорциональна произведению силы токов, длине проводников и обратно пропорционально расстоянию между ними:
где I1, I2; - силы токов, протекающих по проводникам;
r - расстояние между ними;
l- длина проводников;
α- коэффициент пропорциональности.
Если одним проводником сделать катушку, другим - заготовку и соединить их электрически, то при подаче импульса напряжения через конденсатор в катушке возникнет магнитное поле, которое будет действовать на заготовку с силой F. Схема электродинамического способа показана на рис. 9-1.
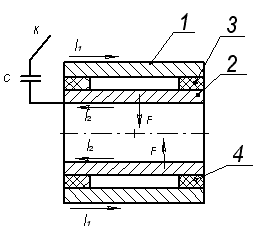 |
Рис. 9-1. |
I1, I2 - токи в катушке (1) и заготовке (2), С - конденсатор, 3 -кольцевая перемычка, обеспечивающая электрический контакт, 4 - диэлектрическая кольцевая вставка.
Силы F, действующие на заготовку, изменяют ее профиль по любой форме матрицы, вставленной внутрь заготовки. Если изменить схему так, чтобы катушка была внутри заготовки, тогда матрицу необходимо надеть на заготовку, при этом будут действовать растягивающие заготовку силы.
При индукционном способе заготовка не является частью электрической цепи. Токи, наведенные в ней электромагнитным полем, взаимодействуют с полем. Силы взаимодействия осуществляют деформацию заготовки по форме матрицы.
Плотность магнитной энергии (рц), действующей на заготовку определяется выражением:
где μо - магнитная постоянная, равная 4π 107, гН/м. Плотность энергии пропорциональна давлению, действующему на заготовку. Величину давления можно рассчитать по выражению:
где Р - давление, кг/см2;
Вмах - максимальное значение индукции в импульсе, Тс. Энергия магнитного поля определяется индуктивностью катушки (L) и силой тока (I) согласно выражения:
Скорость деформации заготовки зависит от величины магнитной индукции и плотности материала заготовки:
где d - плотность материала заготовки, г/см3
Толщина заготовки h должна быть больше глубины проникновения магнитного поля в материал δ, определяемой выражением:
где ρ - удельное сопротивление материала,
τ - длительность полуцикла импульса тока.
При магнитном формообразовании энергия магнитного поля расходуется на создание давления и на нагревание заготовки.
Повышение температуры поверхности заготовки на глубине проникновения магнитного поля определяется величиной поля и удельной теплоемкостью (ср) материала согласно выражения:
Нагрев заготовки оказывает сильное влияние на ее деформацию. В некоторых случаях заготовка разогревается до 1000 - 3000 К. Подбором условий обработки можно изменять соотношение между механической и тепловой составляющими воздействия и создать условия обработки заготовок из материалов, не проявляющих пластичности при нормальной температуре.
В таблице 9-1 приведены значения электрического сопротивления и глубины проникновения магнитного поля для некоторых металлов и сплавов. Из таблицы следует, что с увеличением удельного электрического сопротивления возрастает глубина проникновения магнитного поля, а с увеличением частоты она уменьшается. Для различных материалов, в зависимости от частоты, глубина проникновения изменяется от десятых долей до десятков миллиметров.
Таблица 9-1 Значения электрического сопротивления проникновения магнитного поля материалов.
Материал | ρ 106, Ом/м | Глубина проникновения (мм) при частоте разрядов, кГц. |
1 | 10 | 20 | 50 |
Серебро Медь Золото Алюм. сплав АДМ Латунь Л96 Бронза Бр А5 Углерод, сталь 20 Титан, сплав ВТ51 | 1.6 1.78 2.2 2.92 4.3 9.95 24.2 138 | 2.01 2.12 2.36 2.72 3.3 5.02 6.0 18.7 | 0.64 0.67 0.75 0.86 1.04 1.59 1.9 5.91 |
0.45 0.48 0.57 0.61 0.82 1.12 1.34 418 |
0.28 0.3 0.33 0.38 0.47 0.71 0.85 2.65 |
1.2. Принципиальная схема установки для магнитно-импульсной обработки
Принципиальная схема установки для магнитно-импульсной обработки по казана на рис. 9-2.
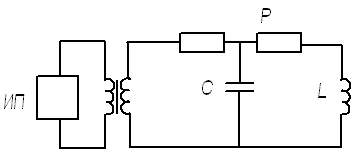 |
Рис. 9-2. Принципиальная схема установки магнитно-импульсной обработки |
Зарядка конденсатора С осуществляется источником тока ИП через трансформатор Тр и выпрямитель В. Разрядка конденсатора на индуктор L осуществляется с помощью разрядника Р. Запасенная в конденсаторе энергия определяется его емкостью и величиной напряжения:
Ток, протекающий в разрядной цепи определяется напряжением и параметрами цепи. Сила тока изменяется со временем по закону:
где L - индуктивность разрядной цепи, R - активное сопротивление разрядной цепи, ω- круговая частота тока разряда .
Амплитудное значение напряженности магнитного поля, создаваемого в индукторе зависит от электрических параметров цепи и формы индуктора и определяется выражением:
где г и 1 - радиус и длина индуктора соответственно. K1 -коэффициент, зависящий от формы индуктора и скорости затухания колебаний в контуре и изменяющийся от 0 до 2.
Длительность полуцикла импульса давления обратно пропорциональна частоте тока импульса и для трубчатой заготовки может быть определена выражением
где Д - диаметр заготовки, 1 - величина зазора между индуктором и заготовкой с учетом глубины проникновения магнитного поля, k2 -коэффициент пропорциональности.
Глава вторая. Технологические операции, выполняемые магнитно-импульсным способом
2.1. Особенности магнитно-импульсного формообразования
Магнитно-импульсные технологии имеют ряд особенностей, отличающих их от других технологий.
1. Метод наиболее эффективен для материалов с высокой электропроводностью, обеспечивающей низкие тепловые потери и достаточно высокий КПД.
2. Диэлектрические материалы данным методом не обрабатываются, так как они прозрачны для магнитного поля. Поэтому камеры для обработки удобно изготавливать из пластмасс или стекол.
3. Толщина заготовки должна быть больше глубины проникновения магнитного поля в материал заготовки, но не слишком большой для данного значения электромагнитных сил.
4. Поскольку инструментом является магнитное поле, то отсутствует механическое сопротивление с деталью, что позволяет обрабатывать заготовки с защитно-декоративными покрытиями.
5. Благодаря высоким скоростям обработки и наличию значительного выделения тепла в заготовке возможна обработка твердых и маловязких материалов - материалов, не обладающих достаточной пластичностью при обычных скоростях и температурах.
6. Значительная часть энергии превращается в тепло в зарядной и разрядной цепях, в самой заготовке. Поэтому КПД процесса низкий и составляет 10-40 % , он зависит от материала заготовки ( плотности, электропроводности) и соотношения габаритов (радиуса и толщины).
2.2. Инструмент для магнитно-импульсной обработки
Рабочим инструментом для магнитно-импульсной обработки является индуктор. Индукторы бывают однократного и многократного использования.
Индукторы однократного использования применяют в единичном производстве, они разрушаются под действием первого импульса магнитного поля, поэтому не должны обладать повышенной прочностью, а должны быть просты в изготовлении и дешевы. Они представляют собой обычно один или несколько витков изолированной проволоки или шины.
Индукторы многократного использования бывают одновитковые, многовитковые и представляют собой спирали, изолированные от корпуса. Одновитковые Индукторы обладают высокой механической прочностью, но они не позволяют получить высокую индукцию. Многовитковые индукторы более эффективны в работе, но они сложнее в изготовлении и дороже. Так как индукторы многократного использования подвергаются ударным нагрузкам, то они должны обладать высокой механической прочностью. Поскольку у них должна быть и высокая электропроводность в поверхностном слое, то их изготавливают из стали, плакированной материалом с высокой электропроводностью.
Для увеличения прочности индукторов и для придания им универсальности служат концентраторы магнитного поля, помещенные внутрь индуктора. Концентратор магнитного поля представляет собой толстенную втулку из высокопрочного материала, обладающего хорошей электропроводностью (например, из бериллиевой бронзы), с разрезом вдоль образующей, заполненным изоляцией, для предотвращения образования вихревых токов. По площади заготовки магнитное поле может быть равномерным или сконцентрированным на определенном участке с помощью металлических концентраторов, изменяющих плотность магнитных силовых линий.
На рис. 9-3 показана схема концентрирования магнитного поля.
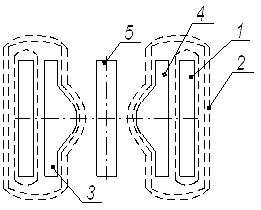 |
Рис. 9-3. Схема концентрирования магнитного поля |
Концентрирование магнитных силовых линий (1), созданных индуктором (2) в области (3) концентратором (4) и заготовкой (5).
В реальных установках для деформации заготовок необходимы импульсные магнитные поля 2 105-106 Гс, которые позволяют получить давление 3 103 - 4 104 кГ/см2.
Длительность импульса при этом должна быть 10-20 мкс.
2.3. Штамповка с помощью импульсных магнитных полей
Магнитно-импульсная обработка материалов и сплавов занимает видное место среди импульсных высокоэнергетических методов металлообработки. Штамповка из плоских и трубчатых заготовок нашла широкое применение. По сравнению с другими методами штамповки магнитно-импульсная штамповка обладает рядом существенных преимуществ, основными из которых являются:
а) большая скорость изменения формы обрабатываемого материала,
б) возможность точного регулирования параметров процесса,
в) возможность широко автоматизировать операции процесса,
г) высокая производительность.
Данный метод пригоден для обработки различных металлов и сплавов, но наибольшее применение он нашел для металлов и сплавов с высокой электропроводностью (медь, алюминий и их сплавы). Это связано с тем, что у заготовок с высокой электропроводностью осуществляется прямое формообразование. Для заготовок с недостаточно высокой электропроводностью (например, углеродистые нержавеющие стали) деформирование заготовок осуществляют через передающую среду или промежуточные материалы с высокой электропроводностью ("спутники"), помещаемые на обрабатываемую заготовку.
Существуют различные схемы штамповки труб и плоских заготовок, отличающиеся формой заготовки, местом расположения индуктора ( внутри или снаружи заготовки), наличием или отсутствием эластичной передающей среды. На рис. 9-4 приведены схемы раздачи(а) и обжима (б) труб. При раздаче индуктор (1) вставляется в трубу (2), при обжиме труба находится внутри индуктора.
В обоих случаях магнитное поле создает давление, которое изменяет форму трубы по форме матрицы (3). Аналогично изменяется и форма плоских заготовок. Давление, действующее на деформируемую заготовку при ее обжиме в цилиндрическом индукторе возрастает при уменьшении поверхности, находящейся внутри индуктора, т. е. при уменьшении диаметра и длины заготовки. Максимальное значение этого давления достигается при определенном соотношении глубины проникновения поля в заготовку с ее диаметром и толщиной стенки.
Экспериментально было получено соотношение
устанавливающее математическую зависимость между изменением диаметра заготовки Д, импульсом давления Р, временем его действия t
, шириной формующего участка М, толщиной заготовки η и плотностью материала заготовки d. Здесь к - коэффициент пропорциональности.
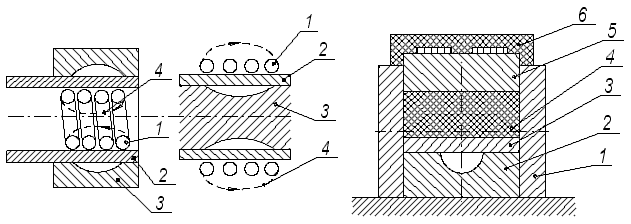 |
Рис. 9-4. Схемы раздачи и обжима труб магнитно-импульсным способом | Рис. 9-5.Схема магнитно- импульсной штамповки |
На рис. 9-5 приведена схема магнитно-импульсной штамповки листового металла через эластичную передающую среду. При данном методе штамповки в толстостенный контейнер 1 помещают металлическую матрицу 2, затем заготовку 3, на которую укладывают блок из эластичного материала 4. Этот блок закрывается подвижной пластиной 5, представляющей комбинацию из электропроводного материала (алюминия, меди и т.д. ) со стороны индуктора 6 и стали или высокопрочного сплава со стороны пластичного материала.
Давление, создаваемое импульсным магнитным полем через подвижную пластину передается на пластичный материал, который вдавливает заготовку в углубление матрицы. В качестве материала для эластичных блоков используют резины определенных сортов и полиуретан. Кроме эластичной среды используют жидкость.
2.4. Сборочные операции, выполняемые с использованием импульсного магнитного поля
Импульсные магнитные поля позволяют производить соединение деталей, которое отличается от механических способов рядом преимуществ.
1. Можно соединять трубчатые детали с деталями самой различной формы.
2. Исключается опасность повреждения наружной поверхности из-за отсутствия соприкосновения детали с инструментом.
3. Процесс сборки легко поддается автоматизации.
4. Качество сборки не зависит от квалификации оператора. Наиболее распространенной операцией сборки деталей является соединение двух трубчатых деталей обжимом наружной трубы по внутренней стороне или соединение трубчатой детали со стержнем таким же способом. Этот способ позволяет соединять детали из разных материалов, что невозможно или затруднено выполнить методом обычной сварки. Повышение прочности соединения достигают нарезанием кольцевых канавок на внутренней или обеих деталях.
Другой областью применения магнитно-импульсного метода является напрессовка и пайка наконечников на концы кабелей. Алюминиевые проводники под действием высокого давления деформируются, принимая шестигранную форму. Если проводники предварительно облужены, то одновременно с опрессовкой может производиться пайка наконечника с кабелем.
Прочность соединения методом обжима зависит от величины зазора между деталями и от шероховатости поверхностей. Величина зазора, обеспечивающего максимальную прочность составляет примерно 0,3 мм, при больших и меньших его значениях прочность соединений уменьшается. С ростом шероховатости в диапазоне 10-49 мкм прочность соединения увеличивается.
Магнитно-импульсным методом осуществляют напрессовку алюминиевых наконечников на фарфоровые изоляторы. Поскольку в такой технологии легко контролировать и поддерживать на необходимом уровне ударную нагрузку, то операции осуществляют без повреждения хрупкого фарфора.
Данный метод применяют для опрессовки шлангов высокого давления, опрессовки наконечников на канаты, соединения проводов трубкой. Широкое распространение получила сварка деталей магнитно-импульсным способом. Этот вид сварки похож на холодную сварку давлением, так как в структуре сварного соединения отсутствуют деформации поверхностных слоев в свариваемых деталях.
Такая сварки применяется при изготовлении теплообменных аппаратов, где необходимо соединять трубы между собой или трубы с трубными решетками, выполненными из разнородных металлов. Прочность сварного соединения также как и при обжиме возрастает с увеличением шероховатости поверхности.
Другой возможной областью применения магнитно-импульсной сварки является ядерная энергетика: приварка заглушек из сплава, плохо поддающегося сварке обычными методами, к оболочкам топливных элементов из сплавов с большим электрическим сопротивлением:
R= 3 мкОм/см у сплава SАР, R = 74 мкОм/см - у сплава "циркалой -2". Результаты исследования структуры и механических свойств сварного соединения сплава "циркалой-2" показали, что изменений твердости не происходит, а испытания на растяжение и сжатие, выполняемые при 733 К и скорости деформирования 0,2 мм/мин, показали преимущества магнитно-импульсной сварки по сравнению с электросваркой.
Возможна диффузионная сварка энергией магнитного поля, Процесс сварки состоит из двух стадий:
- индукционного нагрева соединенных деталей,
- последующего сжатия деталей магнитным полем. Частота тока зависит от толщины деталей. Так, для плакирования труб с толщиной стенки 0,6 мм, менее 5 мм и более 5мм оптимальная частота тока составляет 450, 10 и 1-3 кГц соответственно.
ЧАСТЬ X. ЭЛЕКТРИЧЕСКАЯ СВАРКА
Глава первая. Дуговая электрическая сварка
1.1. История развития электрической сварки
Сваркой называется способ получения неразъемного соединения с обеспечением сплошности соединяемых поверхностей нагревом до температуры плавления или пластического состояния. Этому определению подчиняются все виды сварки, кроме холодной сварки, сварки, где соединение осуществляется за счет взаимной диффузии материала деталей на предварительно очищенных поверхностях при приложении высокого давления.
По виду энергии, используемой для нагрева соединяемых деталей различные виды сварки можно разделить на химическую и электрическую сварку. Наиболее распространенным видом электрической сварки является дуговая сварка, при которой необходимая тепловая энергия выделяется в дуговом разряде, поддерживаемом между электродом и свариваемыми поверхностями.
Дуговая электрическая сварка была изобретена в 1882 году Бенардосом Н. Н., который открыл способ соединения и разъединения металлов посредством электрической дуги, горящей между свариваемым металлом и электропроводящим электродом. В качестве электрода Бенардос Н. Н. использовал угольные электроды, источником постоянного тока служили аккумуляторные батареи. Кроме этого открытия Бенардос Н. Н. изобрел автоматы для сварки угольным электродом, дуговую сварку с защитным газом, дуговую резку под водой и точечную сварку угольными электродами.
Не меньших достижений в области дуговой электросварки добился русский инженер Словянов Н. Г., который открыл в 1988 году способ дуговой сварки металлическим электродом, разработал специальные сварочные генераторы, указал на необходимость применения специальных защитных добавок (марганца, кремния и др.) к расплавленному металлу.
К концу XIX столетия в мире работало около 100 установок дуговой сварки, из них 10 в России. Большой вклад в создание отечественного электросварочного оборудования в 30-е годы внесли профессора Никитин С. П. и Хренов К. К., создавшие оригинальные по тому времени источники тока для электросварки.
Центром научной и технической мысли, центром создания навесного оборудования в бывшем СССР был институт электросварки
АН УССР, созданный академиком Патоном Е. О. и носящий его имя, а в настоящее время возглавляемый его сыном - академиком Б. Е. Патоном. Во время Великой Отечественной войны были созданы и внедрены установки для скоростной автоматической сварки под слоем флюса, сыгравшие большую роль в создании оборонной техники. В последующие годы была внедрена электрошлаковая сварка, электроннолучевая сварка и другие разработки.
1.2. Классификация электрической сварки
Электрическая сварка имеет к настоящему времени очень много разновидностей, определяемых условиями сварки. Ее можно разделить на два подтипа: сварку плавлением и сварку давлением. Сварка плавлением бывает четырех видов: наиболее распространенная дуговая, шлаковая, электронно-лучевая и плазменная. Сварка давлением бывает контактная и диффузионная. В свою очередь дуговая сварка может производиться с использованием плавящихся и неплавящихся электродов. При использовании плавящихся электродов защита от окисления осуществляется под слоем флюса, наносимого на свариваемые поверхности или на электрод, а также в углекислом газе. При использовании неплавящихся электродов в качестве защитной среды применяется аргон. Контактная сварка бывает трех видов: стыковая, точечная и роликовая.
1.3. Дуговая электрическая сварка плавлением
Электрическая сварка плавлением является наиболее широко распространенным способом сварки. Электрическая дуга является высокотемпературным источником тепла, которое используется для оплавления свариваемых деталей. При горении дуги происходит термическая ионизация газа. Степень ионизации зависит от температуры дуги и от рода газа, который в свою очередь определяет потенциал ионизации. Чем меньше потенциал ионизации газа, тем выше степень ионизации. Потенциалы ионизации химических элементов зависят от строения электронных оболочек и изменяются примерно от 3 до 25 В. Наименьшим потенциалом ионизации обладают щелочные металлы, затем идут щелочно-земельные, наибольший потенциал ионизации у газов, а среди них - у инертных газов. В таблице 10-1 приведены значения потенциала ионизации некоторых элементов.
Таблица 10-1 Потенциалы ионизации химических элементов
Элемент | Cs | K | Ca | Ti | Ni | Fe | H | O | N | Ar | He |
V1, B | 3.87 | 4.33 | 6.1 | 6.8 | 7.64 | 7.83 | 13.5 | 13.6 | 14.5 | 15.7 | 34.5 |
Из таблицы следует, что наименьший потенциал ионизации у щелочного металла цезия, наибольший - у инертного газа гелия. Поскольку в сварочной дуге всегда присутствует несколько газовых и металлических атомов, то результирующий потенциал ионизации будет иметь какое-то промежуточное от всех других значение. Причем, установлено, что это значение определяется наличием атомов с наименьшим потенциалом.
Так, при смеси 5 атомов калия (V1= 4.33 В) и 95 атомов железа (V1=7.38 В) результирующий потенциал будет близок к потенциалу ионизации калия. Этим объясняется тот факт, что в обмазку электродов и в флюс присадки для полуавтоматической сварки добавляют элементы с малым потенциалом для повышения устойчивости горения дуги особенно на переменном токе.
Между температурой дуги и эффективным потенциалом ионизации существует линейная зависимость, эмпирическая формула которой установлена академиком К. К. Хреновым:
Для средних значений потенциала 5-410 В температура столба дуги составляет 4000-8000 К.
Сварочная дуга в зависимости от условий проведения сварки может иметь различную зависимость напряжения на столбе от тока -характеристику дуги. Обычно такая зависимость имеет два участка, резко падающий первый участок и почти линейный второй и называется жесткой характеристикой. 1а рис. 10-2 показана эта зависимость.
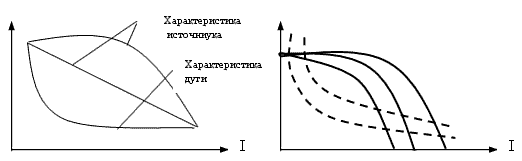 |
Рис. 10-2 | Рис. 10-3 |
Источник питания также имеет свою внешнюю характеристику, представляющую зависимость напряжения источника от тока нагрузки. Эта характеристика также падающая, причем может быть линейно или сверхлинейнопадающей. На рис. 10-2 показаны такие зависимости. Для устойчивого горения дуги необходимо совпадение этих характеристик. В нашем случае в точке К и вблизи нее будет устойчивое горение дуги. Поскольку при сварке толщина деталей может быть самой различной, то и источник питания должен иметь серию внешних характеристик. Тогда в зависимости от сварочного тока требуется различная длина дуги и работа будет производиться по той или иной характеристике источника питания и по соответствующим характеристикам дуги. На рис. 10-3 показана серия таких характеристик.
Таким образом, основными требованиями источника питания дуговой сварки являются: 1) соответствие внешней характеристики источника питания характеристике дуги, 2) наличие возможности регулирования сварочного тока, т. е. наличие серии характеристик и их совпадение.
Третьим требованием к источникам питания является то, что напряжение холостого хода источника должно быть выше напряжения зажигания дуги. Напряжение зажигания дуги при сварке на постоянном токе составляет 50-60 В. Соотношение между рабочим током и током короткого замыкания составляет
Время восстановления напряжения от нуля до напряжения дуги не должно превышать 0,03 секунды.
Сварочное оборудование характеризуется повторно-кратковременным режимом работы. При этом существуют понятия времени работы t1 и времени перерыва t2 также продолжительности включения ПВ, которая определяется соотношением:
Эта величина определяется в процентах и указывается в паспорте. Например, запись 1=250А, ПВ=50% означает, что при токе 250А продолжительность включения составляет 50%. Во время работы обмотка источника тока нагревается, в перерыве она охлаждается, но от цикла к циклу температура растет. На рис. 10-4 показано изменение температуры и тока обмотки со временем работы источника.
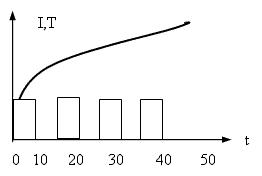 |
Рис. 10-4. Изменение температуры обмотки от времени работы источника |
Видно, что температура после 1,2,3 циклов повышается, а затем стабилизируется. Эта температура и является рабочей температурой обмотки источника питания.
Глава вторая. Специальные виды дуговой сварки
2.1. Аргонодуговая сварка
Сущность данного метода сварки заключается в том, что дуга горит между концом электрода и свариваемым изделием в среде защитного инертного газа - аргона. Помимо защиты от вредного воздействия окружающей среды аргон выполняет несколько положительных функций:
- способствует улучшению устойчивости горения дуги из-за меньшего катодного падения напряжения, чем в воздухе;
- из-за меньшей теплопроводности аргона уменьшаются тепловые потери столба дуги, что также приводит к увеличению устойчивости горения дуги;
- при разряде в аргоне происходит катодное распыление металла, что приводит к его очистке, в частности от оксидов, например от оксида алюминия и улучшению качества шва.
Технические данные аппаратов для аргонодуговой сварки приведены в таблице 10-2. При горении дуги возникает термоэмиссия с катода.
Таблица 10-2 Технические характеристики аппаратов аргонодуговой сварки
Тип аппарата | Основное назначение | Толщина детали, мм | Род тока | Номин. ток, А | Диаметр электрода, мм |
УДАР-300 | Сварка алюминиевых сплавов | 1-12 | ~ | 300 | 2-6 |
УДАР-500 | Сварка нержавеющей стали | 1,5-20 | ~ | 500 | 2-10 |
АГВ-2 | Автоматическая сварка различных металлов | 0,8-16 | = | 400 | 2-6 |
АВТ | Автоматическая сварка труб из нержавеющей стали | 0,5-10 | = | 250 | 1-3 |
Это явление нежелательное, поэтому для увеличения тепловой мощности дуги применяют обратную полярность. Кроме того, при прямой полярности расплавленная ванна металла покрывается пленкой окиси, что препятствует сплавлению деталей. Поэтому аргонодуговую сварку ведут на переменном токе или на постоянном токе обратной полярности. При сварке на переменном токе в схему включается осциллятор для облегчения зажигания дуги и для повышения устойчивости ее горения.
Аргонодуговая сварка производится с плавящимся и неплавящимся вольфрамовым электродом. Чаще используется неплавящийся вольфрамовый электрод. При работе на постоянном токе применяются обычные сварочные генераторы с баластными реостатами РБ-200, РБ-300, включаемыми последовательно в сварочную цепь для регулирования сварочного тока при малых значениях и для обеспечения устойчивости горения дуги. Максимальный сварочный ток некоторых горелок составляет А) ГРАД-200-250, ГРАД-400-400, ЭЗР-3-58-100, АР-10 малая-120, АР-10 большая-400. Напряжение холостого хода 130-200В.
2.2. Дуговая сварка в углекислом газе
Сущность этого метода заключается в том, что в зону сварки с постоянной скоростью подается электродная проволока диаметром 0,5-2 мм в струе углекислого газа (рис. 10-5). Роль углекислого газа состоит в защите расплавленного металла от окружающей среды. С целью уменьшения окисляющего действия углекислого газа электродная проволока имеет повышенное содержание раскисляющих элементов (марганца, кремния).
Данный способ сварки особенно эффективен для сварки металлов небольших толщин порядка 1-2 мм и особенно для швов сложной конфигурации, так как их сварка другими способами, например под флюсом, затруднена или вообще невозможна закрытия шва слоем флюса.
Сварка в углекислом газе выполняется в полуавтоматическом ил» автоматическом режиме. Для этого используются источники постоянного тока:
- преобразователи ПСО - 300, ПС-500, ПСМ - 1000 и др,
- выпрямители ВС - 200, ВС - 300, ВС - 500,
- генераторы типа ГРС.
Горелки для полуавтоматической сварки бывают двух типов:
- для сварки на малых токах без водяного охлаждения (до 300 А).
- для сварки на больших токах с водяным охлаждением. Для сварки используется углекислый газ, получаемый из углекислоты, транспортируемой в черных баллонах с желтой надписью "СО2 сварочный" емкостью 40 л, в который заливается 12,7 м3 углекислоты, дающей при испарении 25 кг углекислого газа. Если использовать пищевую углекислоту, то ее необходимо осушать, для этого между баллоном и редуктором устанавливается осушитель газа.
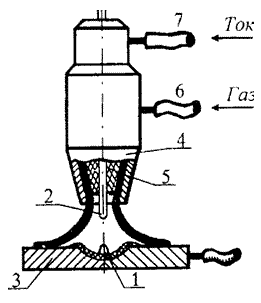 |
Рис. 10-5. Схема сварки в углекислом газе. 1 - расплавленный металл, 2-электрод, 3-свариваемые детали, 4- горелка, 5- керамическая насадка, 6- штуцер для подачи газа, 7- токоввод |
Наилучшие результаты получаются при сварке различных видов сталей и особенно при работе на постоянном токе обратной полярности. В этом случае уменьшается разбрызгивание металла, уменьшается устойчивость горения дуги.
2.3. Электрошлаковая сварка
Принцип данного вида сварки заключается в том, что расплавление электродного металла и свариваемых деталей осуществляется за счет протекания электрического тока через расплавленный флюс (шлак), обладающий электропроводностью. Этот вид обеспечивает сварку деталей большой толщины, доходящей до 2,5м, что невозможно осуществить другими способами сварки.
Свариваемые детали заключаются в медные водоохлаждаемые ползуны и нижнюю (начальную) и верхнюю(конечную) планки, служащие одновременно для начала и окончания шва. Шлаковая ванна формируется внизу, в колодце, образованном свариваемыми деталями, держателями и нижней планкой. По мере сваривания деталей медные держатели поднимаются вверх со скоростью, равной скорости образования шва.
Шлаковая ванна образуется или прямым пропусканием тока через шлак и предварительным нагревом шлака в отдельной установке и последующим заливом его в колодец. При этом обеспечивается устойчивое горение дуги. На устойчивость горения дуги влияет также внешняя характеристика источника, которая должна быть жесткой или
несколько возрастающей - с увеличением тока в ванной напряжение должно быть или неизменным, или возрастать.
Электроды могут быть проволочными, пластинчатыми или ленточными. Может быть один или несколько электродов. Наиболее распространенные аппараты с одним и тремя электродами, хотя могут быть (и имеются) аппараты с 9 и 18 электродами. Данные некоторых аппаратов электрошлаковой сварки приведены в таблице 10-3.
2.4. Электронно-лучевая сварка
Принцип электронно-лучевой сварки заключается в концентрированном нагреве соединяемых деталей за счет использования кинетической энергии ускоренных электронов в высоком вакууме. В результате бомбардировки электронным пучком кинетическая энергия превращается в теплоту, используемую для осуществления сварки плавлением.
Для осуществления этого вида сварки необходимо получить свободные электроны, сфокусировать их в тонкий пучок и ускорить до необходимой энергии. Все это осуществляется в устройстве, называемом электронной пушкой. Свободные электроны получаются из накаленного катода, а ускорение осуществляется при прохождении электронами электрического поля высокой напряженности между катодом и анодом. Фокусировка пучка осуществляется специальной магнитной линзой, а его отклонение в заданном направлении или сканирование по определенной программе осуществляется отклоняющими катушками.
Таблица 10-3 Технические характеристики аппаратов электрошлаковои сварки
Тип аппарата | Толщина деталей, мм | Номин. ток | Uраб, В | Кол-во элек-в | Диаметр электрода |
А-306А: Сварка прямолинейных | 20-60 | 800 | 40 | 1 | 3-5 |
А-372Р: Сварка прямолинейных и | До 450 | 300 | 45-55 | 3 | 3 |
А-741: Сварка прямолинейных и переменной кривизны стыков | До 2500 | 9000 | 36-55 | 3 | 3 |
Этот способ сварки имеет ряд существенных достоинств перед другими, главными из которых являются следующие:
1. Плотность поступающей в зону энергии можно очень точно регулировать, что позволяет широко варьировать глубину провара толщину свариваемых изделий.
2. Возможна сварка деталей любой конфигурации, поскольку электронный луч легко управляется с помощью электрических и магнитных полей, то возможна сварка деталей любой конфигурации.
3. Околошовная зона имеет очень незначительную толщ] поэтому при сварке практически не происходит нагрев свариваемых деталей.
4. Возможность фокусировки пучка электронов до микрон) размеров позволяет использовать этот вид сварки для целей микроэлектроники, радиотехники.
5. Сварка в вакууме исключает любое окисление свариваемых. деталей. Это позволяет соединять детали из весьма тугоплавких материалов, таких как молибден, вольфрам, что недоступно для других способов сварки.
Недостатком данного способа является наличие вакуумных насосов и вакуумных систем, а также сложность устройства и технологии, ] требует высококвалифицированного обслуживающего персонала.
Параметры некоторых типов установок для электронно-лучевой сварки приведены в таблице 10-4.
Таблица 1 Технические характеристики аппаратов электронно-лучевой сварки
Тип установки | Диаметр камеры | Длина камеры | Uкв, В | I, мА |
ЭЛУ4 Общие виды сварки | 700 | 1200 | 60 | 35 |
У-74: Сварка труб | 800 | 1000 | 40 | 75 |
У-101 Сварка труб | 500 | 500 | 25 | 500 |
Конструкционной основой электронно-лучевой сварки являете вакуумная камера на которой сверху монтируется электронная пушка.
Камера имеет герметические вводы дли подачи энергии, подачи охлаждающей воды, передачи движения к находящимся внутри механизма перемещения свариваемых деталей. Камера откачивается форвакуумными и высоковакуумными насосами для создания разряжения не выше 10-3 Па.
Ток пучка, а значит и мощность нагрева можно регулировать как изменением тока накала катода и плотности тока ускоренных электронов, а также ускоряющим напряжением. Катоды пушек могут быть прямонакаленные вольфрамовые в виде спиралей или нитей или подогревные, состоящие из подогревного катода и подогревной таблетки. Подогревные катоды обычно изготавливаются из гексаборида лантана, дают значительно большую плотность тока, чем прямонакальные. Но они более сложны в изготовлении.
2.5. Плазменная сварка
Плазменная сварка и плазменная резка основаны на создании плазменного столба или плазменной струи - потока высокоионизированных частиц с большим запасом энергии, позволяющим достигать температуры 20000К.
Для создания потока ионизированных частиц используется дуговой разряд между двумя электродами в продуваемом инертными газами канале, стенки которого охлаждаются водой. За счет охлаждения внешней части плазменного столба, он концентрируется в центре канала, что приводит к высокой степени ионизации газа и концентрации в нем большой энергии. Эта энергия и используется для сварки или резки металлов.
Источниками питания плазменного сварочного аппарата являются сварочные генераторы постоянного тока или сварочные выпрямители. Возбуждение дугового разряда осуществляется осциллятором, включаемым параллельно источнику тока, а регулирование сварочного тока осуществляется балластным сопротивлением, включаемым последовательно источнику тока.
Мощность плазменной горелки существенно зависит от состава газа. Например, смесь 86% гелия и 14% аргона дает мощность в 2 раза большую, чем при использовании чистого аргона, что объясняется более высоким потенциалом ионизации гелия. Длина яркосветящегося ядра плазменной струи может меняться от 2 -3 до 40 -50 мм в зависимости от геометрии канала, состава и скорости подачи газа, тока и напряжения дуги.
Плазменная струя нашла наиболее широкое применение для резки металлов, не поддающихся обычным способам резки, например, для резки нержавеющей стали, меди, алюминия, керамики. Обычно используется смесь аргона с водородом, концентрация которого может достигать 30%. Плазменной струёй можно сваривать металлы и неметаллы, а также их сочетания. В таблице 10-5 приведены параметры установок плазменной сварки.
Таблица 10-5 Технические характеристики установок плазменной сварки
Тип установки | Назначение | Uхх,В | Номин. ток, А | Wпотр, кВт |
УПСР-300-2 | Сварка нерж. стали до 5мм | 65 | 300 | 16 |
А-1255 | Сварка мет. и сплавов до 1мм | 55 | 10 | 0,8 |
А-1326 | «____»____» | 80 | 30 | 2,5 |
Глава третья. Контактная сварка
3.1. Контактная сварка или сварка сопротивлением
Этот вид сварки относится к одной из разновидностей сварки давлением, при которой детали механически сжимаются для получения соединения и в месте стыка каким-то образом подводится энергия, используемая для разогрева свариваемых деталей. При контактной сварке или сварке сопротивлением энергия выделяется за счет пропускания тока через свариваемые детали и выделения тепловой энергии на большом сопротивлении контакта. Если сами детали не являются практически сопротивлением электрическому току, то место стыка представляет большое сопротивление и вся выделяемая на нем тепловая энергия идет на разогрев деталей.
Контактная сварка бывает трех разновидностей, определяемых геометрией шва и электродов: стыковая, точечная, роликовая. На рис. 10-6 показаны эти типы сварки. Во всех случаях переходное сопротивление контакта может быть определено выражением
где К1 - коэффициент, зависящий от материала контакта деталей;
Fk - усилие сжатия контакта; m- коэффициент, учитывающий форму поверхностей контактирующих деталей; Кt- коэффициент, учитывающий температуру контакта.
где α - температурный коэффициент сопротивления материала,
Т - температура контакта.
При Т близкой к комнатной Кт можно принять равным единице.
Значение коэффициента К1, для различных пар свариваемых деталей следующее:
АL-АL-0,006; Сu-Сu-0,0004; АL-Сu-0,001 сталь-сталь-0,0076; Аg-Аg-0,0006; латунь-латунь-0,00067
Значение m для контакта плоскость - плоскость равно единице, для контактов сфера - сфера и сфера - плоскость m=0,5.
Из этих численных значений коэффициентов следует, что чем лучше контакт, тем больше m, меньше К1 и тем меньше сопротивление.
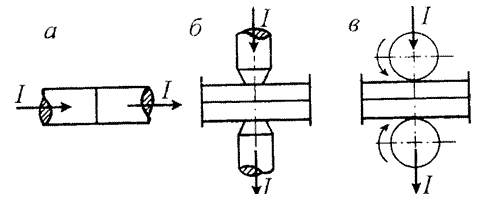 |
Рис. 10-6. Основные разновидности контактной сварки: а - стыковая, б - точечная, в - роликовая. 1-направление сварочного тока |
3.2. Стыковая сварка
При стыковой сварке торцы свариваемых деталей приводятся в соприкосновение, после чего через них пропускается ток, место стыка разогревается до необходимой температуры и продольным сжатием достигается сплошность соединений - осуществляется пластическая сварка. По окончанию цикла сварки ток выключают и снимают усилие.
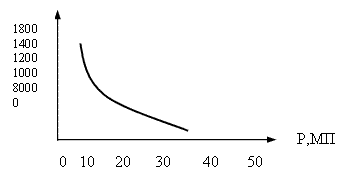 |
Рис. 10-7. Зависимость усилия сжатия от температуры разогрева при стыковой сварке малоуглеродистой стали |
При стыковой сварке два параметра взаимосвязаны друг с другом -температура стыка и сжимающие усилие. Чем выше температура, тем меньше требуется усилие. На рис. 10-7 такая зависимость приведена для малоуглеродистой стали.
Стыковая сварка бывает двух видов: без оплавления (сварка сопротивлением) и с оплавлением. В первом случае нагрев торцов осуществляют только пропусканием тока. Токи очень большие, достигают 5-10кА, удельная мощность составляет 10-15 кВт/см2. Соединяемые детали в этом случае, как правило, небольшого поперечного сечения. Во втором случае сварка производится в несколько стадий: предварительный подогрев, оплавление и окончательная осадка. Вначале усилие составляет 5-20 МПа, затем включается ток и происходит разогрев места стыка до 900-1100 К, после этого сжимающие усилие снижают до 2-5 МПа, что приводит к увеличению сопротивления контакта и снижению тока. В это время контакт осуществляется на небольшой площади, на выступающих остриях, где температура повышается до температуры плавления и выступы исчезают. Затем такой же процесс происходит на следующих выступах и т. д. Очередные выступы разогреваются также за счет теплопроводности.
Происходит перегрев металла на выступах, его парообразование, выбрасывание пара и частиц жидкого металла из зоны стыка. Часть жидкого металла стекает вниз.
|