ОБЩИЕ СВЕДЕНИЯ ОБ ЭЛЕКТРОТЕХНОЛОГИЯХ
Преимущество электротехнологий перед другими методами обработки материалов
Общая классификация электрофизических и электрохимических методов обработки материалов
ЧАСТЬ I. ЭЛЕКТРОЭРОЗИЙНАЯ ОБРАБОТКА МАТЕРИАЛОВ
Глава первая. Физические основы электроэрозийной обработки
1.1. История развития электроэрозийной обработки
1.2. Физические процессы при электроэрозийной обработке
1.3. Основные стадии и закономерности электроэрозийной обработки
1. 4. Материалы для электрода-инструмента
1. 5. Тепловые процессы при электроэрозийной обработке
Глава вторая. Технологические процессы изготовления деталей и показатели ЭЭО
2.1. Схемы электроэрозийной обработки
2.1.1 Прошивание отверстий и полостей
2.1.2. Электроэрозийное шлифование
2.1.3. Электроэрозийное разрезание заготовок
2.1.4. Электроэрозийное упрочнение деталей
2.1.5. Производительность электроэрозийной обработки
2.1.6. Точность ЭЭО
Глава третья. Электроэрозийное оборудование
3.1. Компоновка оборудования
3.2. Генераторы импульсов
3.3. Регуляторы подачи электрода-инструмента
3.4. Системы очистки и подачи рабочей жидкости
ОБЩИЕ СВЕДЕНИЯ ОБ ЭЛЕКТРОТЕХНОЛОГИЯХ
Под электротехнологиями понимаются способы обработки материалов, в которых электрическая энергия используете непосредственно как инструмент для обработки. Эта энергия может выступать в виде дугового или тлеющего разряда, в виде искры, в виде плазмы, в виде электрического поля, в виде высокого напряжения, в виде пучков заряженных частиц (электронов и ионов), в виде концентрированных пучков света, в виде токов высокой частоты. В соответствии с этим, к методам электротехнологий относятся электроискровая, электроэрозийная и электроимпульсная обработка; различные виды электросварки, основанные на действии дуговых разрядов и контактном нагреве; плазменная, электронно-лучевая и ионная обработка; лазерная обработка, электровзрывная и магнитно-импульсная обработка, обработка токами высокой частоты, электрохимическая и ультразвуковая обработка.
Некоторые из этих видов обработки применяются самостоятельно, другие - совместно с механической обработкой. Исключением из перечисленных электротехнологий, не подчиняющихся общему правилу, являются ультразвуковая, электровзрывная и магнитно-импульсная обработки, в которых не электрическая энергия выступает в качестве рабочего инструмента, а механическая энергия ультразвуковых колебаний и энергия ударных волн.
Преимущество электротехнологий перед другими методами обработки материалов
Электротехнологии часто называют новыми технологиями. Они обладают рядом существенных преимуществ перед традиционными (механическими) методами обработки материалов.
1. Возможность обработки материалов с любыми свойствами без применения значительных механических усилий
Такая возможность открывается в связи с тем, что съем материала происходит не путем механических усилий, а посредством действия электроэнергии в различных ее видах, поэтому механические характеристики материала не играют роли.
Например, при электроэрозийной обработке из-за высокой температуры разряда любой материал (металл, диэлектрик, полупроводник) плавится и испаряется. При электрохимической обработке, вне зависимости от типа соединения, агрегатного состояния, происходит растворение, осаждение или другой процесс независимо от механических свойств. Возможность выполнения сварки керамики и металла стала осуществимой в связи с использованием для этих целей электронного луча.
Это преимущество электротехнологий приобрело значимость в последние десятилетия в связи с разработкой новых материалов, обладающих особыми свойствами.
2. Отсутствие необходимости в специальных инструментах или образивах более твердых, чем обрабатываемый материал
В процессе обработки с применением электрохимических и электрофизических методов инструмент как таковой вообще отсутствует (электронно-лучевая, лазерная обработка) или между инструментом и обрабатываемой деталью специально создается зазор, в который поступает электролит (электроискровая, электроэрозийная обработка), и только в некоторых случаях (ультразвуковая размерная обработка) применяется механическое усилие для обработки.
В новых технологиях удельная подводимая мощность очень высокая за счет малой площади взаимодействия и импульсного характера обработки. Это приводит к выделению большой тепловой мощности и достижению высоких температур в местах обработки, что позволяет осуществлять операции, невозможные при обычных методах.
3. Значительное сокращение расхода материала
Это преимущество особенно большое значение имеет при обработке редких и дорогостоящих материалов, таких как рубин, кварц, алмаз, полупроводниковые кристаллы. Экономия получается при их резке, шлифовании, распиловке, фрезеровании за счет оптимального раскроя, меньших по толщине швов.
4. Высокая точность изготовления деталей
В технике часто требуются детали, обработанные с высокой точностью. При использовании электротехнологий, точность обработки в пределах единиц микрометров является вполне достижимой. В то же время при механической обработке такая точность достигается с трудом.
5.Высокая производительность и экономическая эффективность
В некоторых технологических операциях обычные способы механической обработки достигают своих предельных возможностей. В то же время, применение электротехнологий позволяет получить высокие показатели. Например, при обработке твердых и хрупких материалов трудоемкость и длительность значительно меньше, чем при механической обработке. Электротехнологии позволяют значительно увеличить плотность энергии, вводимой в зону обработки. При этом не требуется пропорционального увеличения затрат на оборудование, оснастку и инструмент.
6. Возможность частичной или полной механизации и автоматизации процессов обработки
Позволяет сократить обслуживающий персонал, повысить производительность.
7. Улучшение условий труда
Проведение операций без применения значительных физических усилий приводит к меньшей степени усталости оператора. Квалификация оператора может быть ниже по сравнению с обычной механической обработкой. Квалификация наладчика оборудования и программиста должна быть значительно выше.
Однако электротехнологии, наряду с большим комплексом положительных технических, технологических и экономических показателей, имеют ряд недостатков и ограничений. Это, прежде всего высокая энергоемкость процессов, которая проявляется при изготовлении деталей простой конфигурации и формы. Необходимость применения специального оборудования.
Методы электротехнологии тем выгоднее применять, чем сложнее форма обрабатываемой детали, чем тверже материал и труднее дается обработке резанием, чем выше специальные требования предъявляются к детали или изделию. Этими положениями определяется общая принципиальная направленность методов электротехнологий, преимущественно используемых при создании образцов новой техники, при внедрении новых материалов и новейших достижений науки и техники в практику.
Общая классификация электрофизических и электрохимических методов обработки материалов
Электротехнологии можно классифицировать по нескольким признакам, таким как виды воздействия на обрабатываемую деталь, разновидности выполняемых операций, области промышленности, в которых используются технологии. По виду воздействия на материал, технологии основаны на химическом, тепловом, механическом действии электрического тока. В табл. 1-4 приведена такая классификация.
Таблица 1 Классификация электротехнологии по виду воздействия электрического тока
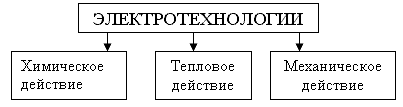
Таблица 2
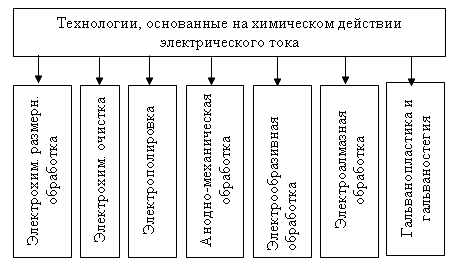
Таблица 3
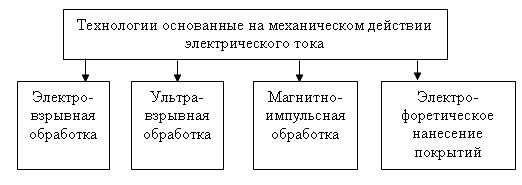
Области возможного применения электрофизических и электрохимических методов обработки материалов
Каждая из приведенных выше электротехнологий находит широкое применение во многих областях техники. Одни и те же операции можно выполнять различными технологическими приемами, выбор которых определяется требованиями к качеству обработки. Приведем возможные операции, выполняемые с помощью этих технологий.
1) Электрохимическая размерная обработка применяется в следующих операциях:
- точного профилирования сложных по форме изделий из труднообрабатываемых материалов (лопатки турбин);
- изготовления фасонных полостей в труднообрабатываемых материалах (пресс-форм и матриц штампов);
- резки твердых материалов;
- изготовления сеток;
- изготовления профиля зубьев;
- сверления отверстий.
2) Электрохимическое травление применяется для:
- очистки металлических поверхностей от окалины;
- очистки поверхности от ржавчины и других загрязнений;
- удаления измененных слоев с поверхности металлов и сплавов;
- повышения качества режущего инструмента;
- клеймения и маркировки.
3) Электрополирование применяется для:
-декоративной отделки поверхностей черных и цветных металлов;
- повышения коррозийной стойкости поверхности;
- улучшения электрических и магнитных свойств;
- снижения коэффициента трения;
- повышения стойкости режущего инструмента;
- округление острых кромок,
4) Электрообразивная и электроалмазная обработка, чистовая иодно-механическая обработка используются как:
- чистовое отделочное и притирочное шлифование и доводка поверхности металлических и металлокерамических изделий;
- окончательная заточка и доводка твердосплавного инструмента;
- полирование изделий из черных и цветных металлов и сплавов.
5) Черновая анодно-механическая обработка применяется при:
- резке металлических заготовок и изделий любого профиля из материалов любой твердости и вязкости;
- вырезке фасонных деталей из листового материала;
- обдирке и черновом шлифовании;
- предварительной заточке режущего инструмента.
6) Нагрев в электролите позволяет осуществлять:
- операции термической и термохимической обработки (закалка, отжиг, цементация);
- плавку;
- пайку;
- упрочнение поверхности.
7) Электроэрозийная обработка (электроимпульсная, электроискровая) применяется в следующих операциях:
- получения полостей и отверстий в металлах и сплавах любой твердости;
- получения отверстий криволинейной и спиральной формы;
- резке металлов;
- нанесения упрочняющих покрытий;
- заточки твердоплавкого инструмента;
- шлифования твердых сплавов;
- нарезания резьб на твердоплавких изделиях;
- изготовления металлических порошков;
- маркировки, гравирования, росписи по металлу.
8) Ультразвуковая обработка применяется для:
- очистки поверхностей;
- размерной обработки твердых сплавов и неметаллических материалов (прошивка отверстий и плоскостей, профилирование вырезка);
- интенсификации практически любых технологических операций (гальванических, химических, металлических, физик химических, механического резания и шлифования, облегчение пайки и лужения активных металлов), обработки давлением, металлизации неметаллических поверхностей;
- сварки пластмасс и неметаллических материалов.
9) Электронно-лучевая обработка используется для:
- плавки металлов и сплавов;
- сварки металлических и неметаллических деталей;
- резки материалов;
- испарения;
- прошивки любых материалов, в т. ч. тугоплавких и сверхтвердых.
10) Ионная обработка используется при:
- легировании полупроводниковых материалов;
- создании энергетических барьеров;
- легировании поверхностных слоев инструмента;
- нанесении упрочняющих слоев;
- создании металлокерамических переходов.
11) Светолучевая обработка применяется при:
- сварке материалов;
- резке материалов;
- прошивке отверстий;
- проведении металлургических процессов с металлическими и неметаллическими материалами любой твердости и тугоплавкости.
12) Плазменная обработка применяется в следующих операциях:
- плавки;
- сварки;
- резки;
- прошивки отверстий и изготовления фасонных изделий и материалов любой твердости;
- нанесения покрытий;
- металлизации поверхности неметаллических материалов.
13) Электрогидравлическая обработка используется для:
- дробления и измельчения твердых и хрупких материалов;
- наклепа металлических поверхностей;
- обработки давлением.
14) Электровзрывная обработка применяется в операциях:
- штамповки;
- очистки;
- дробления материалов;
- получения специальных порошков;
- получения неразъемных соединений.
Основные характеристики электротехнологических процессов
К основным характеристикам электротехнологических процессов относятся: род тока, его частота, величина напряжения, плотность тока, сила тока, длительность импульса, способ подвода напряжения (прямой или косвенный).
Ток может быть постоянный или переменный, в некоторых операциях применяется тот и другой. Частота тока колеблется от промышленной, равной 50 Гц до сотен Герц, килогерц и мегагерц. Напряжение изменяется от единиц Вольт до сотен киловольт. Сила тока изменяется от десятых долей до 104 Ампера. Длительность импульса изменяется от 10-5 с до непрерывного значения. Напряжение в большинстве технологических операций подводится напрямую, но в некоторых (электронно-лучевые, светолучевые процессы, ионная имплантация) оно подводится косвенно.
ЧАСТЬ I. ЭЛЕКТРОЭРОЗИЙНАЯ ОБРАБОТКА МАТЕРИАЛОВ
Глава первая. Физические основы электроэрозийной обработки
1.1. История развития электроэрозийной обработки
Электрическая эрозия является вредным явлением, возникающим на различных контактах электрических устройств - реле, рубильников, выключателей. Она приводит к разрушению контактов и сокращению их сроков службы. Поэтому много исследований было посвящено изучению этого явления и разработке способов борьбы с ним.
В годы II мировой войны над этой проблемой работали советские ученые Б.Р. Лазаренко и Н. И. Лазаренко. Они, изучая явление электрической эрозии металлов, пришли к заключению, что его можно использовать для обработки материалов. Это изобретение имело выдающееся значение в технике обработки материалов, поскольку к традиционным методам механической обработки (резанию, шлифованию, сверлению) добавлялся новый метод, основанный на явлениях в электрических разрядах. Авторы изобретения были удостоены Государственной премии СССР.
В последующие годы электроэрозийная обработка успешно развивалась, схемы усовершенствовались, показатели улучшались. В этом большая заслуга принадлежит отечественным ученым и инженерам Б. Н. Золотых, А. Л. Лившицу, Л. С. Палатнику и другим.
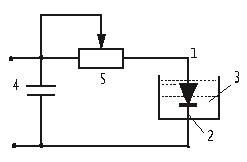 |
Рис. 1-1 Схема установки Лазаренко Б. Р. |
Схема первой экспериментальной электроэрозийной установки Лазаренко Б. Р. и Лазаренко Н. И. показана на рис. 1-1. На помещенные в жидкий диэлектрик 1 электрод 2, являющийся инструментом, и электрод 3, являющийся обрабатываемой деталью, подавался импульс напряжения от конденсатора 4. Зарядку конденсатора осуществляли от источника постоянного напряжения, время зарядки регулировали реостатом 5.
Принцип работы схемы заключается в следующем. При подаче импульса тока на электроды 2 и 3 между ними создается электрическое поле, напряженность которого зависит от межэлектродного расстояния. При сближении электродов между ними возникает разряд, который приводит к разрушению материала заготовки детали. Капли металла охлаждаются диэлектрической жидкостью и в виде шариков удаляются из межэлектродного промежутка. Таким образом, основными элементами первой схемы ЭЭО были: генератор импульсов, конденсатор, реостат, источник напряжения, электрод - инструмент, обрабатываемая деталь и жидкий диэлектрик.
1.2. Физические процессы при электроэрозийной обработке
Удаление металла с заготовки осуществляется за счет микроразрядов, возникающих в среде диэлектрика между инструментом и заготовкой и разогревающих их поверхностные слои. Эти - процессы происходят при сближении электрода - инструмента и заготовки, в результате чего напряженность поля Е увеличивается по закону.
где U - напряжение между электродами,
d - расстояние между электродами.
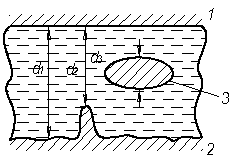 |
Рис. 1-2. Схема расположения инструмента (1), заготовки (2) и токопроводящего включения (3); d1-наибольшее расстояние; d2 -наименьшее расстояние; d3-размер включения. |
Наибольшая напряженность возникает на тех участках, где имеются выступы или где в зазоре находятся какие-либо проводящие включения. На рис. 1-2 показана схема расположения инструмента, заготовки и диэлектрического промежутка. Наибольшее расстояние между электродом-инструментом 1 и заготовкой 2 равно d1 наименьшее d2. За счет токопроводящего включения 3 расстояние d1 уменьшается на величину d3.
При сближении электродов до величины зазора, равного критическому, происходит пробой межэлектродного промежутка и возникает электрический разряд. Металл заготовки нагревается за счет бомбардировки его частицами разряда.
Если заготовка является анодом, то она бомбардируется электронами, а на электрод - инструмент движутся ионы. Поскольку скорость движения этих частиц при одинаковом напряжении определяется их массой, согласно выражения
где m, V, q - масса, скорость и заряд заряженной частицы, соответственно, и - ускоряющее напряжение, то электроны будут достигать поверхности заготовки быстрее, чем ионы достигнут поверхности электрода - инструмента.
Электроны будут разогревать поверхность заготовки, и расплавленный металл будет вылетать из заготовки, охлаждаться диэлектрической жидкостью в зазоре и в виде шариков удаляться вместе с жидкостью из зазора. В результате образуется углубление в виде лунки. Затем пробой возникает в другом месте, где расстояние достигает критического значения dкр и там происходит удаление металла. Таким образом происходит выравнивание поверхности заготовки и удаление металла.
Для того чтобы меньше разрушался электрод - инструмент при подаче на него отрицательного напряжения (прямое включение полярности) необходимо подбирать такую длительность импульса, при которой ионы не будут успевать достигать катода за время действия импульса. Такой способ обработки называется электроискровым,
Но при малой длительности импульса скорость обработки будет уменьшаться, уменьшаться будет и производительность. Поэтому длительность импульса подбирают такой, чтобы и скорость обработки была достаточной и износ электрода - инструмента был мал.
Если необходимо иметь большие скорости съема материала заготовки, то следует увеличивать длительность импульса и поменять полярность: положительный потенциал подать на инструмент, отрицательный - на заготовку. Тогда под действием ионов разряда интенсивно будет разрушаться заготовка, а на инструмент будут идти электроны. Такая схема включения будет называться электроимпульсной обработкой.
При электроэрозийной обработке напряжение составляет 40-180В в электроискровом способе и 18-136В - в электроимпульсном способе. Напряженность поля в межэлектродном промежутке в момент пробоя достигает 107В/м, в зоне разряда образуется плазма, скорость нарастания тока в которой составляет 105А/с. Длительность импульса тока при черновой обработке деталей составляет от 200 до 105 мкс, а при чистовой -от 5 до 200 мкс. Величина тока достигает от 20 до 100 А при черновой и от 0,5 до 50 А при чистовой обработке соответственно.
1.3. Основные стадии и закономерности электроэрозийной обработки
Можно выделить три стадии электроэрозийного процесса:
I. I. Нагрев, оплавление металла, образование лунки.
II. П, Образование газового пузыря из паров металла и жидкости.
III. Ш. Расширение газового пузыря, отрыв ударной волны от газового пузыря и ее гашение жидкостью.
После нагрева, оплавления металла и образования лунки, наступает вторая стадия эрозийного процесса - образование газового пузыря из паров металлов и жидкости. В канале проводимости, образованном в месте возникновения микроразряда, создается высокое давление, достигающее значений 2·107 Па. Канал проводимости расширяется, образуется газовый пузырь, который сжимает окружающую газовую фазу. Граница пузыря движется с высокой скоростью, достигающей 22 м/с. Между газовым пузырем и окружающей жидкостью образуется фронт уплотнения, в котором давление скачкообразно меняется от исходного в жидкости до 107Па.
Третья стадия процесса характеризуется прекращением тока между электродами, расширением газового пузыря, отрывом ударной волны от газового пузыря и гашением ее жидкостью. При расширении пузыря давление в нем резко падает и содержащийся в лунках расплавленный металл выбрасывается в межэлектродный промежуток и застывает в виде шариков. Схема третьей стадии показана на рис. 1-3.
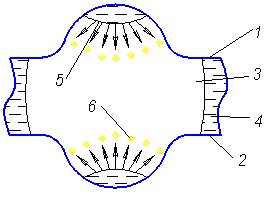 |
Рис. 1-3. Схема третьей стадии электроэрозийного процесса: 1, 2-электроды; 3-газовый пузырь; 4-сжатая жидкость; 5-лунка; 6-расплавленный металл. |
Между электродами 1 и 2 образуется газовый пузырь 3, который, расширяясь, сжимает жидкость 4. Из лунки 5 расплавленный металл 6 в виде шариков выбрасывается в межэлектродный
В качестве жидкостей используют различные диэлектрики: масла, керосин, выполняет двоякую роль - роль диэлектрического промежутка и роль охлаждающей среды. Кроме того, она уносит продукты обработки. Поэтому жидкость прокачивается через промежуток с определенной скоростью. Если же скорость обработки мала, то емкость с жидкостью делают соответствующего объема и жидкость не прокачивается.
Если электроэрозийную обработку проводят в воздушной среде, то вместо электроискрового разряда возникает более длительный электродуговой разряд, поскольку охлаждение менее интенсивное, чем в жидкости. Такой способ обработки называется электроконтактным. Схема электроконтактной обработки показана на рис. 1-4.
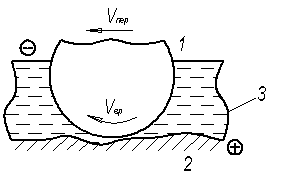 |
Рис. 1-4. Схема электроконтактной обработки: 1-инструмент; 2-деталь; 3-диэлектрик; Vпер-скорость перемещения; Vвр-скорость вращения инструмента. |
Между электродом - инструментом 1 и деталью 2 находится диэлектрик. Поверхности электродов имеют выступы и не являются идеально гладкими. Поэтому при сближении до определенного значения dкр возникает разряд. Если обработка ведется в воздушной среде, то возникают длительные дуговые разряды. Выплавляются большие участки заготовки. Поскольку зазор между электродами в такой схеме обработки мал, то возможен вариант не только съема металла, но и наращивания материала инструмента на заготовке за счет попадания расплавленного материала инструмента и его застывания на заготовке. Этот процесс называется электроэрозийным легированием.
При электроконтактной обработке напряжение на электродах обычно составляет (1- 2) В и достигает до 12В в воздушной среде и от 8 до 40В в жидкой среде. Существуют три источника тепла, вклад которых зависит от напряжения и скорости вращения электрода-инструмента: механический, дуговой и электрический. Механический определяется скоростью вращения электрода-инструмента, дуговой - напряжением, током и длительностью дугового разряда, электрический сопротивлением в местах электрического контакта.
При электроконтактной обработке при малых напряжениях (1-2) В основной вклад в нагрев дает трение, при напряжении порядка 10В нагрев идет, в основном, за счет дугового разряда.
Выбрасывание расплавленного металла в электроконтактном способе осуществляется подвижным электродом-инструментом, который помимо вращения перемещается по поверхности заготовки.
Большим достоинством электроконтактного способа является возможность осуществления легирования заготовки и ее упрочнения. Поскольку: материал электрода-инструмента (анода) не переносится на заготовку (катод), то происходит их взаимодействие и образование новых сплавов в поверхностном слое. При этом образуются нитриды или карбиды - слои с высокой износостойкостью. Происходит также диффузия материала анода в более глубокие слои заготовки.
1. 4. Материалы для электрода-инструмента
Критериями выбора материалов для электрода-инструмента
- эрозийная стойкость,
- удельная проводимость,
- прочность,
- коррозийная стойкость,
- возможность изготовления инструмента требуемой формы с минимальными затратами, - стоимость.
По эрозийной стойкости, в порядке ее возрастания, материалы можно расположить в ряд: алюминий и его сплавы, серый чугун, латунь, медь, вольфрам, графитовые материалы.
Эрозия материала зависит от теплопроводности и температуры плавления. При постоянной энергии импульса нагрев тем меньше, чем больше теплопроводность, так как тепло быстрее уходит внутрь материала. Поэтому электроды-инструменты выполняют обычно из меди, латуни, алюминия, поскольку их эрозия меньше, чем эрозия твердых сплавов и стали. В то же время материал должен иметь высокую температуру плавления. Поэтому для изготовления электрода-инструмента иногда применяют графит, вольфрам, композиции меди и вольфрама. Чаще же применяют электроды из меди и латуни, так как они более дешевы и могут быть изготовлены любой формы.
Наиболее интересным решением вопроса о повышении износостойкости инструмента является процесс нанесения (осаждения) на поверхности слоя углерода, образующегося в результате разложения углеродосодержащей рабочей жидкости. При равенстве скоростей износа и осаждения слоя форма и размеры инструмента будут постоянными в процессе работы. Этого можно достичь подбором особой формы импульса напряжения: с крутым передним фронтом, необходимым для обеспечения разряда и гребенчатым задним фронтом, необходимым для разложения рабочей жидкости и выделения углерода. Примером является такое осаждение углерода на медь. Износостойкость повышается в десятки раз.
1. 5. Тепловые процессы при электроэрозийной обработке
Приближенный расчет температуры в окрестности разряда производят при следующих предположениях:
- разряд является стационарным источником теплоты,
- теплофизические характеристики электродов и межэлектродного промежутка являются постоянными во времени.
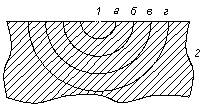 |
Рис. 1-5. Схема распространения тепла в материале заготовки: 1-точечный источник тепла; 2-заготовка. |
Схема распространенна теплоты в материале заготовки показана на рис. 1-5.
Точечный источник тепла 1 излучает энергию во все стороны, но большая ее часть из-за малых размеров попадает на электрод - заготовку 2. Изменение температуры заготовки определяется выражением:
где Q - безразмерный параметр температуры, учитывающий теплопроводность заготовки λ. и время действия импульса энергии τ;
Р - энергия импульса;
с - удельная теплоемкость материала заготовки;
р - плотность материала заготовки;
r - расстояние от источника тепла до точки определения температуры;
η - коэффициент полезного действия импульса энергии.
Коэффициент полезного действия импульса энергии определяется выражением:
где k1 - коэффициент, учитывающий потери энергии на нагрев жидкости, образование газового пузыря и ударной волны и равный 0,5 при электроискровом режиме и 0,47 при электроимпульсном режиме;
k2 - коэффициент, учитывающий нагрев электрода-инструмента и зависящий от его теплофизических характеристик и расположения относительно заготовки;
k3 - коэффициент, характеризующий свойства диэлектрической среды, изменяющийся от 0,2 (керосин) до нуля (масла);
k4 - коэффициент, учитывающий изменение напряжения, равный +0,1, если напряжение выше номинального и -0,1, если напряжение ниже нормального.
В качестве примера в табл. 1-1 показана зависимость температуры металла от расстояния от точечного источника по сферическим кривым (изотермы) в конце действия импульса мощностью 0,54 Дж длительностью 8мс.
Таблица 1-1 Зависимость температуры металла от расстояния от точечного источника тепла
г, мкм | 0 | 5 | 10 | 15 | 20 | 30 | 40 | 50 |
Т, К | 5700 | 4850 | 3350 | 2870 | 1850 | 630 | 335 | 296 |
Температура плавления металла равна 1850 К, перегрев до температуры 5700 К необходим для обеспечения его жидкотекучести при выбрасывании из лунки. Глубина лунки при этих условиях составляет 20 мкм.
Глава вторая. Технологические процессы изготовления деталей и показатели ЭЭО
2.1. Схемы электроэрозийной обработки
Технологические схемы электроэрозийной обработки, используемые в промышленности, следующие:
а) прошивание отверстий,
б) разрезание,
в) электроэрозийное шлифование,
г) электроэрозийное упрочнение.
Прошивание - это удаление металла из полостей, углублений, отверстий, пазов. Существует два вида прошивания:
- прямое копирование, когда инструмент расположен над заготовкой,
- обратное копирование, когда инструмент расположен под заготовкой.
Во втором случае облегчается удаление продуктов обработки. Разрезание профильным или непрофильньгм инструментом предполагает разделение заготовки на части - отрезание, или получение непрямолинейного контура - вырезание. Отрезание выполняется пластиной или диском. В обоих случаях инструмент перемещается к заготовке, но диск дополнительно еще вращается.
Электроэрозийное шлифование выполняется с помощью диска, совершающего вращательное и поступательное движения. При этом заготовка может быть неподвижной или вращающейся. Если вращение происходит в одну сторону, шлифование называется попутным, если в разные стороны - встречным.
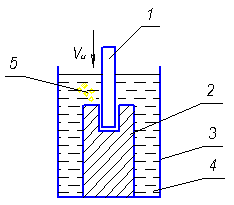 |
Рис. 1-6. Схема прошивания отверстий и полостей: 1-электрод-инструмент; 2-заготовка; 3-ванна; 4-электролит; 5-продукты обработки; Vu-скорость подачи инструмента. |
Электроэрозийное упрочнение происходит как за счет легирования, так и за счет наращивания поверхности. Оно обычно осуществляется при электроконтактном способе, поэтому будет более подробно рассматриваться далее.
2.1.1 Прошивание отверстий и полостей
Схема электроэрозийного прошивания отверстий и полостей показана на рис. 1-6. Между электродом-инструментом 1 и заготовкой 2 подается напряжение и возникает электрический разряд. В ванной 3 электролитом 4 выносятся продукты обработки 5 в виде шариков.
Операции прошивания применяются во многих случаях.
1) Удаление из обрабатываемых деталей обломков метчиков, сверл и других инструментов. В таких случаях используют схему прямого копирования. Для электрода-инструмента применяют медь, латунь, алюминий или его сплавы. Электроэрозийный способ удаления обломков инструмента и крепежа применяется на заключительных операциях, позволяет устранить брак технологического процесса, исключить необходимость отжига детали, который применяют для снижения твердости обломков инструмента.
2) Изготовление деталей из труднообрабатываемых материалов, таких как жаропрочные сплавы, закаленные детали, магнитные сплавы. Для выполнения таких операций производят расчеты режимов обработки (энергию импульса, напряжение холостого хода, длительность обработки, производительность), исходя из условий шероховатости отверстия.
Материалом электрода-инструмента являются графитовые композиции при обработке закаленных, жаропрочных и твердых сталей; при обработке титановых сплавов применяют латунь. Обычно такие операции производят без прокачки рабочей жидкости, но для повышения точности обработки производят прокачку или отсос жидкости.
При прошивании глубоких отверстий возникают трудности, связанные с поддержанием необходимых режимов при значительном внедрении электрода-инструмента в заготовку, так как при этом резко возрастает вибрация инструмента, затруднено удаление продуктов обработки из отверстия.
Конструкция электрода-инструмента зависит от отношения глубины отверстия е к его диаметру d. При е/d<=20 и d<5мм, l<=100мм можно использовать сплошной стержень, но при этом производительность обработки по мере углубления электрода-инструмента в деталь снижается на 10-15 %, При l/d>20 применяют электроды-инструменты в виде трубки из меди, латуни, графитовых материалов. Отверстия позволяют прокачивать или отсасывать рабочую жидкость и сократить время обработки за счет устранения периодического выведения инструмента из углубления. Такая конструкция позволяет получать глубокие отверстия с соотношением l/d=40. Если требуется получить отверстия с l/d>40, то применяют трубки с нарезным спиральным каналом для удаления продуктов обработки, иногда используют вращение инструмента.
3) Прошивание некруглых отверстий и пазов проводят очень часто в тех случаях, когда необходимо такой профиль получать на твердых сплавах. Например, при изготовлении лопаток турбин авиационных двигателей, при изготовлении матриц и штампов, изготовлении каналов и пазов в насосах, турбинах, компрессорах. Электрод-инструмент в таких случаях изготавливают из меди, латуни, чугуна или графитовой сплава. Если профиль отверстия сложный и по длине непрямолинейный то предусматривают поворот электрода-инструмента в процессе обработки.
4) Прошивание соединительных каналов в корпусах гидроаппаратуры трудно выполнимо методами механической обработки. Если же поперечное сечение каналов некруглое, то его получение возможно только с применением электрических методов, в частности электроэрозийным прошиванием.
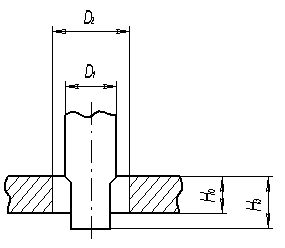 |
Рис. 1-7. Схема сквозной обработки цилиндрического отверстия |
Расчет размеров электрода-инструмента для обработки сквозных или глухих отверстий различной формы приведен в специальной справочной литературе. Здесь мы рассмотрим наиболее простые формы отверстии и формулы для расчета размеров электрода-инструмента.
На рис. 1-7. приведена схема сквозной обработки цилиндрического отверстия.
Здесь обозначено Do, Но - диаметр отверстия и его глубина соответственно, Dэ - размер рабочей части электрода-инструмента в горизонтальной плоскости; Нрэ -длина рабочей части электрода-инструмента.
При такой схеме обработки при однопроходном прошивании отверстий размеры электрода-инструмента определяются выражением:
, (1-5)
где l - боковой межэлектродный зазор, равный 0,35 ÷ 1,48 мм в зависимости от значения максимального тока обработки в импульсе, изменяющегося в пределах 50 - 300 А;
γэ - относительный износ электрода-инструмента, зависящий от его
материала (медь, чугун графитированный), формы и частоты импульсов,
материала заготовки.
Например, при f=22кГц прямоугольных, импульсах е графитированном электроде, при обработке стали, γэ= 3 - 5%; при гребенчатой форме импульсов и тех же параметрах γэ= 0,08 - 0,15%. Если отверстие ступенчатой формы, то формулы для расчета размеров электрода инструмента усложняются (рис. 1-8).
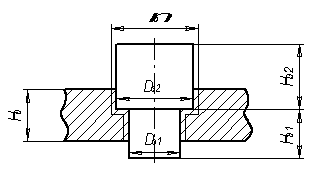 |
Рис. 1-8. Схема сквозной обработки отверстия ступенчатой формы. |
Здесь Δ - допуск на размер отверстия в горизонтальной плоскости;
lτ - торцевой межэлектродный зазор, зависящий от частоты, формы и тока импульсов и изменяющийся от 0,01 до 0,5 мм.
Помимо рассмотренных выше операций, большое место занимают прошивание наружных поверхностей, изготовление сеток, решеток, тонкостенных деталей конструкций, а также маркирование деталей.
2.1.2. Электроэрозийное шлифование
Электроэрозийное шлифование применяют для обработки магнитных слитков, электротехнических изделий, собранных из тонких пластин. Преимущество электроэрозийного шлифования перед механическим заключается в том, что отсутствуют большие нагрузки, исключается скалывание твердосплавных и магнитных материалов.
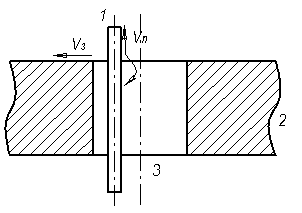 |
Рис. 1-9. Схема шлифования проволочным электродом: 1-электрод-инструмент; 2-заготовка; 3-отверстие; Vп, Vз- скорость подачи и скорость перемещения проволоки и детали соответственно. |
Для шлифования мелких отверстий, например, в твердосплавных фильтрах применяют проволочный электрод, который постоянно протягивается, что исключает влияние его износа на точность обработки. Схема такого шлифования показана на рис. 1-9.
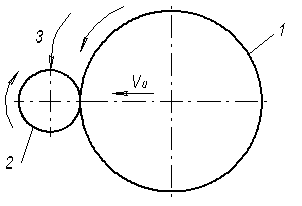 |
Рис. 1-10. Схема встречного шлифования: 1-электрод-инструмент; 2-заготовка; 3-сопло полива жидкостью; VU-скорость подачи инструмента. |
Электрод-инструмент (проволока) 1 вводится в заготовку 2 через предварительно вскрытое отверстие 3. Вращение и передвижение(V3) к стенке отверстия приводит к шлифованию, а передвижение (Vu) проволоки позволяет избежать износа инструмента.
Помимо шлифования проволочным электродом применяется встречное шлифование, схема которого показана на рис. 1-10. В этом случае электрод-инструмент 1, изготовленный в виде диска, и заготовка 2 вращаются в противоположных направлениях. Заготовка поливается рабочей жидкостью, подаваемой через сопло 3. Электрод-инструмент подается с постоянной скоростью Vи к заготовке по мере ее обработки.
2.1.3. Электроэрозийное разрезание заготовок
Разрезание заготовок электроэрозийным способом осуществляют диском или лентой. При разрезании диском заготовка может быть неподвижной или вращающейся. Вращение позволяет повысить производительность в 3 - 4 раза. Если вращения нет, то целесообразно при разрезании толстых заготовок (более 100 мм) заготовку перевернуть после прохождения середины и дальнейшие операции производить с обратной стороны.
Процесс ведут на воздухе или в жидкой среде при токе 600, 800 А. Диск выполняется из листовой стали до 1 мм толщиной и до 1000 мм диаметром. Погрешность достигается не более 0,2 - 0,3 мм. Если разрезается жаропрочная сталь, то время сокращается в 8 -10 раз по сравнению с механическим разрезанием. При разрезании лентой ее толщина небольшая и значительно уменьшить толщину реза. Применяют латунные ленты толщиной 0,1 мм и стальные толщиной 0,3мм. Схема разрезания показана на рис. 1-11. Электроэрозийное разрезание используют в основном производстве для разделения нежестких заготовок, например, тонкостенных трубок. В инструментальном производстве этим методом отрезают заготовки для резцов, штампов из твердосплавных материалов. При изготовлении вырубных штампов фильер, матриц использую!
2.1.4. Электроэрозийное упрочнение деталей
Поскольку в электрическом разряде осуществляется перенос металла, то электроэрозийным методом возможно упрочнение деталей. Оно может быть нескольких видов:
- наращивание значительного слоя металла с целью упрочнения и восстановления изношенных участков деталей;
- нанесение тонких покрытий из благородных металлов, например, для электрических контактов;
- упрочнение за счет изменения физико-механических свойств поверхности без изменения размеров детали.
Современное оборудование для упрочнения позволяет проводить операции в различных режимах - "грубые", "черновые" и "чистовые".
2.1.5. Производительность электроэрозийной обработки
Производительность электроэрозийной обработки определяется отношением массы или объема удаленного металла ко времени обработки и выражается в граммах/с или мм3/с. Она пропорциональна мощности, расходованной в межэлектродном промежутке.
где С - коэффициент, зависящий от теплофизических характеристик материала;
Р - мощность;
А - энергия в импульсе;
f - частота следования импульсов.
Если же производить отрезание заготовки электроэрозийным методом, то такое определение производительности будет неправомерным, поскольку масса снятого материала в этом случае не является критерием операции. Площадь боковой поверхности реза в этом случае является мерой выполненной операции, а ее отношение ко времени обработки - производительностью (S/t). Площадь определяется произведением толщины заготовки на длину реза или площадью круга для круглых заготовок. Производительность легирования с целью упрочнения материала определяется отношением площади нанесенного слоя ко времени обработки:
.
В любом случае производительность зависит от мощности, реализуемой в межэлектродном промежутке. С увеличением мощности увеличивается скорость обработки, но при этом увеличивается и количество продуктов обработки, которые тормозят процесс съема металла. По мере углубления в заготовку, усложняется удаление продуктов обработки и поступление свежей жидкости в межэлектродный промежуток. В межэлектродном промежутке образуется большое количество электропроводных капель застывшего металла и энергия тратится на вторичное расплавление этих частиц. Для их удаления и повышения производительности используют принудительную прокачку рабочей жидкости.
В зависимости от свойств рабочей среды изменяется доля полезного использования энергии импульса. Поэтому для каждого вида обработки применяют оптимальную диэлектрическую среду: если в процессе электроэрозийной обработки используется малая энергия импульса, то применяют дистиллированную и техническую воду или керосин, при больших энергиях импульса применяют масла, дизельное топливо, т. е. тяжелые фракции нефти.
На рис. 1-12 показано влияние состава среды на производительность обработки при прошивке медно-графитовым электродом ферросилида. Видно, что из трех видов диэлектрической жидкости наибольшая производительность достигается при обработке в керосине, наименьшая - при обработке в воде.
Для сравнения эффективности электроэрозийной обработки различных металлов и сплавов введено понятие обрабатываемости, которое определяется отношением массы снятого металла к массе металла, снятого с заготовки стали 45.
2.1.6. Точность ЭЭО
Под точностью электроэрозийной обработки понимается степень соответствия формы и размеров детали чертежу. Отклонение от формы и размеров называется погрешностью.
На точность ЭЭО влияют:
- точность изготовления электрода-инструмента;
- износ электрода-инструмента;
- погрешность формы и размеров углубления на заготовке относительно электрода-инструмента, зависящая от нестабильности режимов обработки, вызванной колебаниями напряжения в сети, изменениями скорости подачи и износом электрода-инструмента.
Износ электрода-инструмента является основным фактором, влияющим на точность обработки. Для большинства режимов обработка он составляет:
- при прошивании сталей в электроискровом режиме медным электродами 30 - 95% от объема снятого металла с заготовки;
- при работе в электроимпульсном режиме медно - графитовым электродами 0,1 - 4%;
- при электроконтактном резании на воздухе до 30%.
Для снижения влияния износа на точность обработки необходимо:
а) изготавливать электрод-инструмент из стойкого к эрозии:
материала (из вольфрама, меднографита и др.);
б) использовать безизносные схемы, в которых часть материала и рабочей среды осаждают на электроде-инструменте, компенсируя тем самым его износ;
в) заменять изношенные участки электрода-инструмента путем его перемещения.
Погрешность при электроэрозийном легировании определяете неравномерностью наносимого слоя и достигает 20% от его толщины.
Глава третья. Электроэрозийное оборудование
3.1. Компоновка оборудования
Станки для электроэрозийной обработки включают - следующие блоки системы:
- генераторы импульсов,
- средства регулирования и управления,
- систему подачи и очистки рабочей жидкости.
 |
Рис. 1-13. Блок-схема электроэрозийного станка |
Блок - схема электроэрозийного станка показана на рис. -1-13. Она включает: механическую часть (1), состоящую из рабочего стола устройства для закрепление электрода-инструмента, системы регулирования и управления; генератор импульсов (2) электрошкаф (3) с размещенными в нем пускателями, рубильниками, предохранителями; ванну с рабочей жидкостью, насосами, фильтрами (4). Электроэрозийное оборудование выпускается или серийно, или по индивидуальным заказам. Он может быть универсальным, специализированным, специальным.
3.2. Генераторы импульсов
В настоящее время известно несколько типов генераторов импульсов: релаксационные, машинные, ламповые, полупроводниковые. Основное требование к генераторам - получение импульсов необходимой формы и мощности. Хронологически первыми были релаксационные генераторы, разработанные Б. Р. Лазаренко и Н. И. Лазаренко. Параметры импульса в этих генераторах определяются состоянием межэлектродного промежутка. На рис. 1-14 показаны 4 типа RС - генераторов. Это RС (а), RLС (б), RCL (в), LС (г) - генераторы. Все релаксационные генераторы имеют зарядную и разрядную цепь. Зарядная цепь включает источник питания ИП, ключ К, токоограничивающий резистор К (в LС - генераторах его нет). Разрядная цепь состоит из межэлектродного промежутка МЭП, конденсатора С и, возможно, индуктивного элемента L.
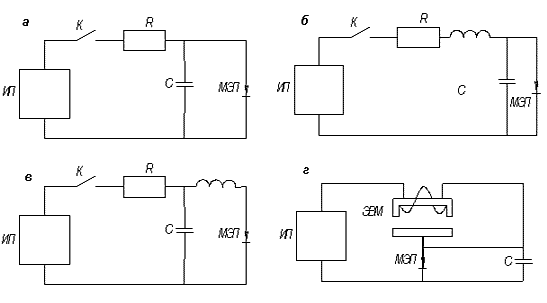 |
Рис. 1-14. Схема RC-генераторов различных типов: а-RC, б-RLC, в-RCL, г-LC |
Принцип работы всех RС - генераторов заключается в зарядке конденсатора до напряжения U от источника питания при замыкании ключа. Постоянная зарядки τ определяется произведением RС. При достижении U, равного пробивному Uпроб, происходит пробой промежутка,
электроэрозийный процесс и разрядка конденсатора.
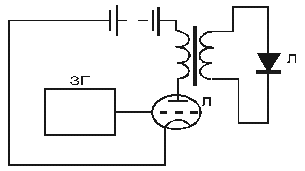 |
Рис. 1-15. Схема лампового генератора импульсов. |
Ток через промежуток прекращается, происходит процесс деионизации промежутка (восстановление диэлектрических свойств среды) и зарядка конденсатора.
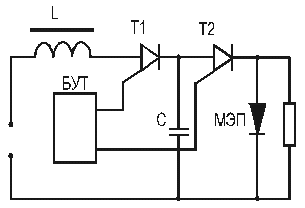 |
Рис. 1-16. Схема полупроводникового генератора импульсов |
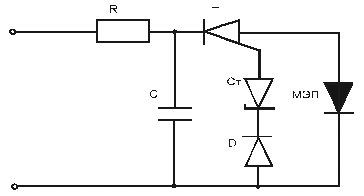 |
Рис. 1-17. Схема генератора импульсов со стабилизатором |
Необходимо, чтобы время зарядки было больше период деионизации τ>Т и чтобы разряд не перешел в дуговой. Это достигаете подбором R и С. Если быстро сближать электроды, то время зарядки уменьшается, разряды будут происходить часто, напряжение и энергия промежутка будут малы. При совсем малых расстояниях время между разрядами будет мало и деионизация промежутка будет недостаточна. Разряд может перейти в дуговой. Таким образом, от состояния МЭП (расстояние между электродами, параметры среды) зависит режим работы генератора.
Обычный RС - генератор имеет малый КПД (25%) и малую мощность (5-7 кВт) из-за нагрева резистора. Повысить мощность за счет уменьшения времени зарядки и повышения напряжения удается введением L-элемента в RLС - генераторах. Но при этом, как и в RС генераторах, возникает обратная полуволна, разрушающая электрод инструмент. Этот недостаток удается устранить в RСL-генераторах. Но при этом понижается мощность. Поэтому такие генераторы используют для чистовой обработки, когда анодом служит инструмент.
С целью повышения КПД разработаны LС - генераторы, в которые исключен ограничивающий резистор, и введен электромагнитный вибратор ЭМВ, якорь которого жестко связан с электродом инструментом. При подаче напряжения ток протекает через обмотку вибратора, якорь притягивается к сердечнику и перемещает инструмент от заготовки.
В это время течет ток через конденсатор С. При достижении Ильного напряжения зарядки сердечником Umax инструмент подходит к загшотовке, промежуток пробивается, ток через конденсатор прекращается, якорь не удерживается, горит разряд, происходит электроэрозийный процесс, конденсатор разряжается. Затем процесс повторяется. Такие генераторы используются для черновой обработки.
Для повышения производительности процесса используются электронные лампы, поскольку в RС - генераторах увеличение энергии импульса связано с возрастанием времени накопления заряда. В ламповом генераторе (рис. 1-15) частота следования -импульсов определяется задающим генератором ЗГ. Частоту следования импульсов удается повысить до 20кГц. Недостатком лампового генератора является низкий КПД, высокое напряжение питания (несколько кВ).
Для получения широкой диапазона режимов обработки используются полупроводниковым генераторы импульсов. Схем генератора показана на рис. 1-16.
При подаче напряжения блок управления тиристорами (БУТ открывает тиристор Т) и ток течет через конденсатор С до его полной зарядки После зарядки БУТ закрывает тиристор Т1 и открывает тиристор Т2. В это время происходит пробой межэлектродного промежутка разрядка конденсаторе Токоограничивающим элементом является катушка индуктивности L, сопротивление Кщ в разрядной цепи позволяет разряжаться конденсатору при разомкнутом МЭП.
Недостатком таких генераторов является нестабильность напряжения пробоя, что приводит к изменение режимов обработки. Для устранения этого недостатка используют схемы со стабилитроном Ст (рис. 1-17). В ней заряд осуществляют через резистор R или катушку индуктивности. В это время тиристор Т закрыт. После зарядки напряжение на конденсаторе становится выше напряжения на стабилитроне Uс >Ucт и стабилитрон открывает тиристор. Происходит разряд со строго дозированной энергией через промежуток.
3.3. Регуляторы подачи электрода-инструмента
Основное назначение регулятора подачи электрода-инструмента поддерживать необходимый размер межэлектродного промежутка 1 течение всего времени обработки. Поскольку величина промежутка мала (десятые доли миллиметра), то регулятор должен обладать высокой чувствительностью, быстродействием. В случае колебаний напряжения или попадания проводящих частиц в межэлектродный промежуток регулятор должен отрабатывать соответствующие команды.
Основными элементами регулятора являются:
-измерительный преобразователь,
-блок сравнения,
-усилитель,
-исполнительный механизм.
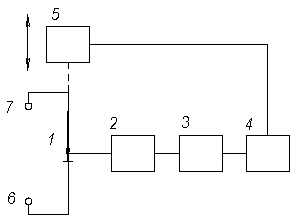 |
Рис. 1-18. Регулятор подачи электрода-инструмента: 1-МЭП; 2-измерительный преобразователь; 3-сравнения; 4-усилитель; 5-исполнительный механизм; 6,7-зажимы для генераторов импульсов. |
На рис. 1-18 показана блок-схема регулятора. Информация о зазоре из МЭП 1 поступает на измеритальный преобразователь 2, откуда в виде электрическое сигнала передается в блок сравнения 3, где происходит его сравнение с опорным сигналом
Вычитание и дальнейшее усиление в усилителе 4 Если сигнал из блока 2 больше опорного сигнала, то исполнительный механизм произведет уменьшение МЭП; если сигнал меньше опорного то исполнительный механизм увеличит зазор.
Регуляторы бывают электрогидравлические и электромеханические. У электрогидравлического регулятора исполнительным механизмом является гидропривод, у электромеханического - электродвигатель. Схема электромеханического регулятора показана на рис. 1-19.
Сигнал из МЭП 1, на который подается напряжение от генератора импульсов 2, подается на делитель напряжения 3. На него же подается и опорный сигнал из блока 4. Если они отличаются, то разностный сигнал подается на электродвигатель 5, который, вращаясь, изменяет межэлектродный промежуток. Направление вращения ЭД определяется знаком разностного сигнала. В этой схеме усилителем - преобразователем является делитель напряжения, т. е. он исполняет роль преобразователя блока сравнения и усилителя, исполнительным механизмом является электродвигатель.
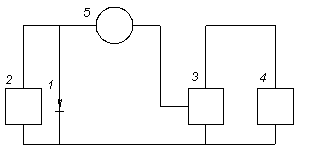 |
Рис. 1-19. Схема электромеханического регулятора: 1-МЭП; 2-генератор импульсов; 3-делитель напряжения; 4-источник опорного напряжения; 5-двигатель. |
3.4. Системы очистки и подачи рабочей жидкости
Рабочая жидкость может находиться в МЭП неподвижно между электродом - инструментом и обрабатываемой деталью или прокачиваться. При прокачке улучшается качество и точность обработки, увеличивается производительность. Для этого предназначена гидравлическая система станка. На рис. 1-20 показана схема такой системы. Из бака 1 насосами 2 через фильтры 4 и устройство регулирования расхода рабочей жидкости Ц- регулятор расхода, 6-конус для сброса, 7-вентиль для сброса) подается рабочая жидкость.
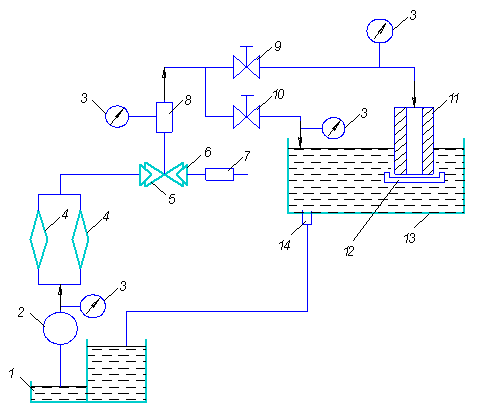 |
Рис. 1-20. Система очистки и подачи рабочей жидкости. |
При этом возникает два варианта подачи рабочей жидкости: либо через полость электрода-инструмента 11 к детали 12 при открытом кране 9, либо через кран 10 непосредственно в рабочую ванну 13. Измерение давления осуществляется манометрами 3, слив жидкости из рабочей ванны в бак 1 осуществляется через отверстие 14. Расход жидкости измеряется ротометром 8.
|