3. Технология монтажа электрических проводок, осветительных и силовых электроустановок, средств автоматизации
3.1. Технология монтажа электрических проводок
3.1.1. Подготовка трасс электропроводок
3.1.1.2. Пробивные работы при установке крепежных деталей
3.1.1.3. Крепежные работы
3.1.1.3.1. Забивка в строительные основания крепежных дюбелей
3.1.1.3.2. Заделка в строительные основания крепежных деталей путем вмазки
3.1.1.3.3. Крепление деталей и изделий к закладным частям
3.1.1.3.4. Крепление с помощью универсально-сборных электромонтажных конструкций
3.1.1.3.5. Приклеивание крепежных деталей и изделий
3.1. Технология монтажа электрических проводок
Современный индустриальный монтаж электропроводок выполняется в две стадии. Первая стадия – это подготовительные и заготовительные работы вне зоны монтажа (в МЭЗ) и непосредственно на монтажных объектах, вторая стадия – прокладка проводов по подготовленным трассам с выполнением всех подключений.
Основной объем монтажных работ производится в МЭЗ, где на специальных технологических линиях заготавливаются узлы электропроводок и целые комплектные линии освещения.
Заготовленные в МЭЗ узлы с материалами, изделиями и деталями, которые необходимы для выполнения всего комплекса работ, укладываются в контейнеры и транспортируются на объект. Контейнеры комплектуют в соответствии с числом этажей, пролетов (или секций) и квартир жилых домов. Стеллажи контейнеров обычно разделяются на отсеки, имеющие маркировку. Если контейнер комплектуется для жилого дома, заготовки укладываются в отсеки по отдельным квартирам в последовательности, отвечающей расположению их по этажам.
Работы первой стадии монтажа непосредственно на объекте состоят из подготовки трасс для прокладки проводов, прокладки заземляющих проводников, установки закладных элементов и деталей для последующего крепления к ним электрооборудования и электроконструкций (если они не были предусмотрены в проекте и не установлены строителями). Эти работы выполняются одновременно с общестроительными работами, но при определенном уровне готовности объекта, т.е. в соответствии с требованиями СНиП при возможности обеспечения нормального и безопасного ведения электромонтажных работ, защиты монтируемого оборудования, кабельных изделий и электроматериалов от влияния атмосферных осадков, грунтовых вод, низких температур, а также от загрязнения и случайных повреждений при производстве дальнейших работ смежными организациями.
До начала работ второй стадии должны быть полностью закончены строительные и отделочные работы в электротехнических помещениях, включая монтаж и испытание отопления и вентиляции-
Электромонтажные работы второй стадии в производственных помещениях производятся одновременно с монтажом технологического оборудования по совмещенному графику.
Отступления от требований к выполнению строительных работ, при которых возможен монтаж электрооборудования, приводят к порче оборудования и электрических сетей, а на их восстановление, очистку, повторную сушку, окраску, ревизию непроизводительно затрачиваются средства и труд.
Борозды, каналы, ниши в стенах и перекрытиях для монтажа проводок и электроконструкций в соответствии с требованиями СНиП должны быть предусмотрены в строительных чертежах и выполнены в процессе строительства или в процессе изготовления панелей и блоков на комбинатах стройиндустрии. Отсутствие каналов и ниш приводит к необходимости выполнения трудоемких пробивных работ.
Здания и сооружения для производства электромонтажных работ второй стадии принимаются от строительных организаций по акту, при этом проверяется соответствие их готовности требованиям СНиП, а также наличие, размеры и число предусмотренных основным проектом или проектом производства работ монтажных проемов для подачи электрооборудования и блоков комплектных устройств.
3.1.1. Подготовка трасс электропроводок
Подготовка трасс электропроводок включает в себя:
– разметку трасс и мест установки крепежных деталей;
– пробивные работы для установки крепежных деталей;
– крепежные работы (установку крепежных деталей в строительных конструкциях – бетонных, кирпичных, шлакоблочных).
Работы по подготовке трасс электропроводок относятся к наиболее трудоемким, особенно при ручном их выполнении.
3.1.1.1.Разметка трасс и мест установки крепежных деталей
Разметка начинается с привязки трасс к местам расположения распределительных устройств, вводов, пусковых приборов и приемников электроэнергии, т. е. сначала размечаются места пробивки отверстий, гнезд и ниш или места установки закладных элементов для закрепления электрооборудования, а затем определяются и размечаются трасса электропроводки, места проходов через стены и перекрытия, установки коробок, а также установки крепежных деталей для труб, кабелей и др.
Для разметки электропроводок применяются специальные разметочные инструменты (рис. 3.1). Трассы открытых электропроводок должны располагаться относительно архитектурных линий интерьера помещения так, чтобы быть менее заметными, т.е. они Должны проходить вдоль, а не поперек лучей света и повторять линии карнизов и других строительных элементов.
Начало электропроводки определяется местом установки электроаппаратов, распределительных устройств и другого оборудования. Затем намечаются уровень трассы электропроводки над чистым полом и все проходы сквозь строительные конструкции, повороты трассы и обходы препятствий. При нанесении разметочных линий руководствуются правилами расположения проводов и кабелей относительно других объектов (ПУЭ). Радиусы поворотов трасс должны быть не меньше минимально допустимых радиусов изгиба проводов или кабелей, применяемых при проводке. При прокладке вертикальные потоки проводов размещаются симметрично оси трассы, а горизонтальные - на нормативном расстоянии от пола (по нижнему проводу). Верхний провод горизонтального потока прокладывается на расстоянии не менее 50 мм от линии карниза или не менее 100 мм от потолка. Радиус поворота потока принимается по максимальному из допустимых радиусов изгиба проводов. Незащищенные открытые электропроводки с напряжением выше 42 В располагают на
высоте не менее 2 м в помещениях с нормальными условиями и не менее 2,5 м в помещениях с повышенной опасностью
и особо опасных. Открытые электропроводки с напряжением до 42 В в любых помещениях
прокладывают на высоте не ниже 2 м. Высота прокладки защищенных проводов (в трубах, коробах,
металлорукавах) не нормируется.
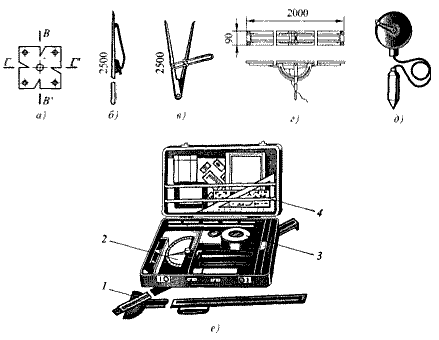 Рис. 3.1. Инструменты для разметки: а – шаблон; б – разметочный шест; в – разметочный циркуль; г – разметочная рама с шестом; д – рулетка-отвес; е – набор разметочных инструментов; 1 – телескопическая линейка; 2 – угломер; 3 – рулетка; 4 – разметочный трафарет
Для тросовых электропроводок производят разметку мест анкерных и промежуточных креплений, для электропроводок на лотках – мест установки поддерживающих конструкций и точек их крепления к строительным элементам зданий, при прокладке проводов и кабелей по полосам и лентам – мест крепления полос, лент и т.д.
При разметке трубных трасс необходимо выполнять точную привязку мест выхода концов труб к электроприемникам. Опорные конструкции для прокладки трубопроводов должны устанавливаться в одной плоскости точно по горизонтальным и вертикальным линиям разметки.
Для этого на трассе проводки или участке трассы устанавливаются две крайние детали крепления и между ними натягивается шнур или стальная проволока, по которым расставляются остальные детали крепления. Вертикальная разметка производится по отвесу.
Расположение трассы и места установки электрооборудования определяются по рабочим чертежам проекта с использованием заданных отметок от уровня пола или потолка, расстояний от колонн, ферм и других строительных элементов, расположенных на одном уровне, или маркшейдерских отметок.
Разметка трасс вертикальных и горизонтальных открытых электропроводок производится с помощью разметочного шнура с соблюдением параллельности линиям сопряжения стен и потолков. Поперечными линиями отмечаются места установки опорных конструкций и крепежных деталей в следующем порядке: сначала у коробок, электроприемников, на поворотах и у проходов, а затем в промежутках между ними. Крепежные детали, поддерживающие и закрепляющие провода и кабели, должны располагаться вдоль трассы симметрично и на одинаковых расстояниях, не превышающих максимально допустимые по СНиП, а проходы – на одной линии и в одной плоскости с прокладываемыми проводами и кабелями.
При разметке трасс прокладки плоских проводов необходимо учитывать следующие требования:
– открытая электропроводка по стенам и перегородкам прокладывается вдоль архитектурных линий (карнизов, балок, линий художественной обработки, выступающих углов), но на расстоянии до 20 мм от них;
– при скрытой прокладке трасса должна легко определяться при эксплуатации проводки, чтобы исключить вероятность ее случайного повреждения (горизонтальные участки трассы располагаются таким образом, чтобы линии сопряжения стен и потолков были параллельны);
– вертикальные участки трассы (спуски или подъемы к светильникам, выключателям и штепсельным розеткам) должны прокладываться параллельно линиям дверных и оконных проемов или углам помещения;
– скрытая прокладка проводов по перекрытиям (в штукатурке, щелях и пустотах плит, под плитами перекрытия) должна выполняться по кратчайшему расстоянию между наиболее удобным местом перехода ее на потолок и светильником.
Разметку трасс скрытых электропроводок, углубленных в борозды стен и потолков, можно производить следующим образом: по кратчайшему расстоянию от вводов до электрооборудования и светильников.
Места пробивки отверстий и гнезд для установки электроконструкций часто намечают с помощью простых разметочных шаблонов (рис. 3.2).
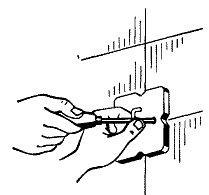 Рис. 3.2. Разметка по шаблону
При сооружении зданий из сборных строительных конструкций с отформованными в них каналами для проводов и проемами, нишами и углублениями для распределительных устройств и электроустановочных изделий разметку мест их установки и трасс электропроводок не делают, а проверяют пригодность каналов для затягивания проводов, особенно в местах сопряжения строительных элементов здания.
Максимальные расстояния между точками крепления, радиусы изгиба проводов и другие требования по разметке трасс электропроводок регламентируются действующими правилами и нормами.
3.1.1.2. Пробивные работы при установке крепежных деталей
Объем пробивных работ и затраты труда на их выполнение при современных индустриальных методах монтажа резко сокращаются благодаря применению прогрессивных способов закрепления деталей и конструкций в строительных основаниях:
– забивки и встреливания крепежных дюбелей;
– установки закладных частей;
– образования каналов, борозд, ниш, сквозных отверстий в строительных конструкциях при их изготовлении;
– приклеивания деталей электропроводок и электроустановочных изделий.
Пробивные работы, которых полностью избежать невозможно, должны выполняться механизированным способом, что сокращает затраты труда и обеспечивает получение правильных геометрических размеров пробиваемых отверстий при минимальном нарушении строительных конструкций.
Основными средствами механизации пробивных работ являются электрические ударные дрели, электрические и пневматические молотки и перфораторы, оснащенные рабочим инструментом (сверлами, бурами, шлямбурами, коронками) с пластинами из твердых износостойких сплавов (в основном из металлокерамических сплавов марки ВК – зерен карбида вольфрама, сцементированных металлическим кобальтом).
Сверление гнезд и отверстий производится главным образом в кирпичных стенах, так как для бетона, даже невысоких марок твердости, оно не эффективно. Производительность в этом случае составляет 10 мм в минуту, а при попадании сверла в твердый наполнитель скорость сверления резко снижается и происходят сильный нагрев, быстрый износ и выкрашивание твердосплавных пластинок.
Для эффективного сверления отверстий в железобетоне используются электроперфораторы и электромолотки с ударно-вращательным действием инструмента, имеющие большую производительность по сравнению с простым сверлением вследствие более эффективного удаления буровой мелочи и требующие меньших усилий для их удержания.
При наличии сети сжатого воздуха для пробивки отверстий больших размеров (особенно в бетонных основаниях) рекомендуется использовать пневмоинструмент – молотки ударного и ударно-поворотного действия (перфораторы), которые отличаются легкостью, простотой конструкции, надежностью и относительной безопасностью.
Отверстия под распорные дюбеля в кирпичных и бетонных основаниях пробивают специальным пробойником ручным или механизированным способом. При ручном способе пробойники вставляются в специальную оправку, при механизированном – в переходную втулку электрического или пневматического молотка. Цилиндрическая рабочая часть пробойника имеет три продольных канавки длиной 55 мм для удаления буровой мелочи.
Ручные пробойники выпускаются только двух типов: ПО-1 длиной 90 мм и диаметром 4,8 мм и ПО-2 длиной 90 мм и диаметром 7,8 мм. Применяются они с оправкой типа ОПКМ с клином, предназначенным для выбивания пробойников из оправки.
Пробивание отверстий вручную производится легкими ударами молотка по пробойнику, который прочно закрепляется в оправке и направляется перпендикулярно к стене. После каждого удара пробойник легко поворачивается. Диаметр пробойника выбирают на 0,5 мм меньше диаметра дюбеля, так как отверстие в стене при пробивании получается на 0,5... 1 мм больше диаметра пробойника. Глубина отверстия должна соответствовать длине дюбеля.
Для пробивки отверстий в многопустотных плитах междуэтажных перекрытий применяется пиротехническая ударная колонка УК-2М.
3.1.1.3. Крепежные работы
Выбор способа крепления при монтаже, если он не предусмотрен проектом, определяется видом строительного основания, характером нагрузки, массой закрепляемой детали, а также трудоемкостью и стоимостью работ.
3.1.1.3.1. Забивка в строительные основания крепежных дюбелей
Дюбеля, надежно закрепляющие изделия в строительных конструкциях, делятся на три группы: распорные для крепления без вмазывания в предварительно подготовленные отверстия (металлические и пластмассовые); встреливаемые строительно-монтажным пистолетом; забиваемые ручной или пиротехнической оправкой.
Самозакрепляющиеся распорные дюбеля используются для крепления без вмазки к кирпичным и бетонным основаниям различных электроустановочных изделий и деталей, применяемых при монтаже осветительных и силовых установок.
Металлический распорный дюбель состоит из корпуса, который представляет собой штампованную или точеную (для болтов диаметром более 6 мм) гильзу из мягкой стали толщиной 8 мм, распорной конической гайки, винта по металлу (с полукруглой, цилиндрической или шестигранной головкой) или болта и двух шайб – нормальной и пружинной. Зубцы и выемки на гильзе и соответствующие этим выемкам ребра на гайке препятствуют вращению гильзы или гайки при ввинчивании винта. Гильза имеет два продольных разреза для более легкого ее распирания гайкой при затяжке, для этой же цели конец гильзы со стороны гайки выполнен с небольшим расширением. Дюбеля с конической распорной гайкой применяются для закрепления легких конструкций, небольших щитков, пусковых аппаратов и др.
Винт и дюбель соединяются с деталью, подлежащей закреплению (скобой, лапкой, ящиком). Затем корпус дюбеля вставляется в подготовленное отверстие и легким ударом молотка забивается так, чтобы его наружный торец был в одной плоскости с краями отверстия. Дюбель должен входить в отверстие с небольшим трением. Винт или болт, пропущенный через отверстие закрепляемого шзделия, ввертывается в распорную гайку до отказа. При ввинчивавши винта распорная гайка, перемещаясь в корпусе дюбеля, распирает своим конусом лепестки корпуса и плотно прижимается к стенкам отверстия, благодаря чему изделие надежно закрепляется. В настоящее время в основном применяются дюбеля из пластмассы (рис. 3.3) и капрона.
Капрон представляет собой твердый материал белого или светло-желтого цвета. Это синтетический материал, получаемый в результате полимеризации капролактама – порошкообразного вещества с температурой плавления 70 °С. У капрона температура плавления 215 °С. Он очень устойчив к плесневым грибкам, но не устойчив к атмосферным воздействиям.
Как и у других полимерных материалов, у капрона наблюдается медленная деформация (холодная текучесть) под действием постоянной нагрузки. Если деформация в пределах 3 %, то после снятия нагрузки она исчезает.
Наибольшее применение капрон получил для производства электромонтажных и конструкционных деталей малой массы.
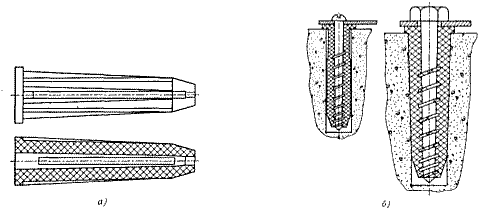 Рис. 3.3. Пластмассовые распорные дюбеля: а – общий вид; б– установленные в строительное основание
Корпус пластмассового дюбеля цилиндрической формы с внутренним конусным каналом разделен на две половины продольной щелью для облегчения расклинивания. Расположенные по длине наружной поверхности дюбеля ребра служат для уплотнения его в гнезде и улучшения сцепления с поверхностью гнезда и препятствуют проворачиванию при ввертывании шурупов.
Пластмассовые дюбеля имеют ряд преимуществ по сравнению с другими дюбелями: они устойчивы к динамическим нагрузкам и вибрациям, высоко устойчивы к коррозии и их можно применять во влажных и химически активных средах. Для закрепления скоб, установочных изделий и небольших конструкций используются дюбеля с шурупами, а для закрепления поддерживающих кабельных и троллейных конструкций, тросовых проводок, аппаратов, струнных подвесок – дюбеля с глухарями.
В настоящее время пластмассовые дюбеля вытесняют металлические.
Разметку мест вбивания дюбелей следует выполнять точно и тщательно, так как в дальнейшем исправить неточность невозможно. В стальных полосах сети заземления и вспомогательных деталях для их прокладки необходимо в местах крепления предварительно просверлить отверстия диаметром 4 мм.
Размер дюбеля выбирается в зависимости от твердости основания и наличия на нем штукатурки: для бетона и железобетона марки 200 и ниже – 2,5 х 25 мм, для красного и силикатного кирпича – 3,5 х 35 мм, а для оштукатуренных оснований (если недостаточно дюбеля 3,5 х 35 мм) – 4,5 х 40 мм. Для проверки правильности выбора (поскольку качество материала основания, от которого зависит длина заглубляемой части, может оцениваться только приближенно) необходимо по месту работ провести пробную забивку нескольких дюбелей.
3.1.1.3.2. Заделка в строительные основания крепежных деталей путем вмазки
Этот трудоемкий способ крепления применяется редко, например при отсутствии закладных частей или если нельзя использовать дюбеля (при креплении тяжелых аппаратов). Вмазка крепежных деталей включает в себя следующие операции:
– выполнение в строительном основании гнезда путем сверления или пробивки;
– очистку гнезда и смачивание его водой;
– заполнение гнезда на одну треть или половину цементным или алебастровым раствором;
– заделку опорной детали в гнездо.
3.1.1.3.3. Крепление деталей и изделий к закладным частям
Для крепления элементов электрооборудования к стенам, перекрытиям, колоннам, фермам и балкам широко используются закладные части, представляющие собой отрезки водогазопроводных труб, листовой, полосовой, угловой или круглой стали, которые устанавливаются в строительных основаниях при сооружении зданий или при изготовлении строительных конструкций на заводах и полигонах в соответствии с рабочими чертежами по заданию организации, проектирующей электрооборудование.
Крепление электрооборудования и устройств электрической сети к закладным частям производится болтами или электросваркой либо через промежуточные переходные детали. В помещениях, которые имеют перекрытия из сборных железобетонных плит, для установки закладных частей целесообразно использовать швы между плитами и места сопряжения отдельных деталей. Для надежности концы закладных частей из профильной стали загибают или приваривают к ним пластины, шайбы и т. п.
При использовании закладных частей для крепления конструкций исключаются пробивные работы, а электромонтажные выполняются после окончательной отделки помещения.
3.1.1.3.4. Крепление с помощью универсально-сборных электромонтажных конструкций
В последнее время разработан и освоен заводской выпуск универсально-сборных электромонтажных конструкций УСЭК, представляющих собой набор унифицированных несущих, соединяющих и крепежных деталей.
Из этих деталей в МЭЗ или непосредственно на объекте собираются без сварки и сверления различные металлоконструкции (кронштейны, подвесы, закрепы), используемые для установки или прокладки различных электротехнических устройств и коммуникаций (шинопроводов, лотков, коробов, осветительной арматуры и др.).
Номенклатура изделий УСЭК включает в себя 35 типоразмеров деталей с болтами, гайками и шайбами, например скобы, уголки, основания, патрубки, профили, полосы, шарниры, прижимы, шпильки, установочные и закладные гайки, клиновые соединители, анкеры. Применение УСЭК для подвески светильников и шинопроводов показано на рис. 3.4.
Крепление с помощью элементов УСЭК сводится к выбору или резке профилей требуемой длины и сборке их с помощью крепежных деталей по типовым альбомам или замерам, при этом сокращаются до минимума механические работы (остается только резка или рубка профилей на мерные отрезки), исключаются операции сварки и нанесения покрытий, упрощается выполнение соединений.
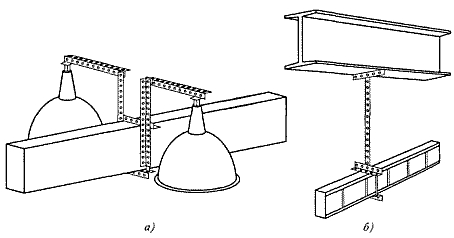 Рис. 3.4. Применение УСЭК для крепления светильников (а) и подвески шинопроводов (б).
3.1.1.3.5. Приклеивание крепежных деталей и изделий
В настоящее время применяется крепление деталей для электропроводок, электроустановочных изделий и мелких конструкций к строительным основаниям с помощью клеев из полимерных материалов. Приклеивание исключает пробивные работы, облегчает условия труда, удешевляет монтаж, сохраняет целость и прочность оснований. Однако до последнего времени этот способ не выходил за рамки опытного внедрения, так как ни один клей полностью не обеспечивал быстрого и прочного соединения. И только применение клея БМК-5К на основе акриловой смолы показало надежность и перспективность этого способа крепления. В состав данного клея входят смола БМК-5 (180 мас. ч.), ацетон в качестве растворителя (420 мас. ч.) и каолин в качестве наполнителя (400 мас. ч.).
В качестве растворителей используются легкоиспаряющиеся жидкости: ацетон, бензол, спирты и др. Ацетон - это бесцветная жидкость со своеобразным запахом, легко воспламеняющаяся, пары ее взрывоопасны. Хорошо смешивается с водой, спиртом, бензином. Применяется для растворения эпоксидных смол и обезжиривания.
Наполнители – порошкообразные или волокнистые вещества, повышающие механическую прочность и уменьшающие объемную усадку пластмассовых изделий. Для повышения механической прочности используются стеклянные, асбестовые и хлопковые волокна, а для повышения коэффициента теплопроводности пластмасс и увеличения их нагревостойкости – кварцевый и слюдяной порошки. Всего в пластмассах содержится 40...60 % наполнителей.
Введение в состав клея наполнителя повышает его прочность и эластичность, снижает усадочные явления и сокращает время отвердевания.
Клей поставляется расфасованным в тубы емкостью 0,1 дм3 или в другую герметически закрываемую тару емкостью до 0,25 дм3. Смешивать раствор смолы с наполнителем непосредственно на рабочем месте не рекомендуется. Клей БМК-5К сохраняет однородность состава даже после длительного хранения, поэтому не требует дополнительного размешивания.
Закрепление проводов, полос заземления и мелких установочных изделий возможно как посредством приклеивания крепежных деталей (рис. 3.5), так и непосредственно самих ответвительных коробок и других пластмассовых изделий, имеющих плоскую опорную поверхность не менее 6 см2.
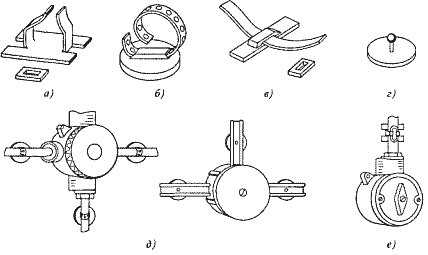 Рис. 3.5. Крепежные детали и установочные изделия для приклеивания: а – деталь из жести с пряжкой; б – деталь из пластмассы или металла в комплекте с поливинилхлоридной лентой и кнопками из полистирола; в - деталь из пластмассы или металла в комплекте с плоской полосой и пряжкой; г – пластмассовая деталь для крепления проводов; д – соединительные коробки; е – полугерметический выключатель.
Перед приклеиванием необходимо подготовить поверхность строительных конструкций, т. е. зачистить место соединения стальным шпателем или стальной щеткой от неровностей и загрязнений. Не допускается приклеивание к побелке, масляной краске, промасленным и закопченным основаниям. Поверхность строительного основания должна быть сухой, ровной и чистой. Стальные поверхности очищают от ржавчины и обезжиривают чистым тампоном, смоченным в ацетоне или бензине марки не ниже М-72. Проверяют также опорные поверхности приклеиваемых деталей и при необходимости очищают их от пыли, жировых пятен и ржавчины, удаляют заусенцы, а металлические детали выправляют для обеспечения плотного прилегания к основанию.
Приклеивание осуществляют в следующем порядке: шпателем-лопаткой клей наносится на строительное основание и по всей поверхности соединения приклеиваемой детали. Нанесенный слой должен быть ровным толщиной 0,5... 1,0 мм; лишний клей снижает прочность соединения. Затем приклеиваемую деталь прижимают с некоторым усилием к опорной поверхности и удерживают в зависимости от массы изделия в течение 2... 5 с. Сила схватывания клея, возникающая при этом, достаточна для удержания изделия. Необходимая для производства дальнейших работ прочность приклеивания достигается через 24 ч. Гарантийный срок хранения клея 9 месяцев. По истечении этого срока клей подлежит повторному испытанию на отрыв.
Приклеивать непосредственно провода или кабели клеем БМК-5К к строительному основанию не рекомендуется, так как из-за быстрого высыхания его консистенция по длине провода будет неодинакова, а следовательно, неодинаковой будет прочность соединения, и, кроме того, при отставании провода у одного конца проводки произойдет отклеивание ее по всей длине без особых усилий.
Минимальная удельная прочность клея БМК-5К при прямом отрыве от бетона, железобетона, керамики – 50 Н/см2, от кирпича – 10 Н/см2. Качество и прочность крепления зависят от правильного приготовления клея и соблюдения технологии приклеивания.
При испытаниях, а также на основе опыта внедрения клея БМК-5К установлены следующие ограничения: не следует приклеивать им детали, подвергающиеся ударным нагрузкам и сильной вибрации (из-за хрупкости клея), и использовать его в сырых помещениях (прачечных, банях). После затвердевания клей БМК-5К остается водостойким, прочность его слоя уменьшается незначительно; в сырых помещениях отклеивание происходит из-за снижения прочности поверхностного слоя строительного основания вследствие намокания. При соприкосновении с водой жидкий клей БМК-5К свертывается и теряет свои свойства, поэтому нельзя приклеивать детали к сырым основаниям.
Затвердевший клей морозостоек, но жидкий он не пригоден для использования при низких температурах, т. е. его можно применять только при плюсовой температуре. Не рекомендуется приклеивать электроустановочные изделия к гипсолитовым, гипсобетонным, оштукатуренным мокрым способом строительным конструкциям и сухой штукатурке, имеющим недостаточную прочность поверхностного слоя.
Клей обладает хорошей адгезией (прилипанием поверхностей двух разнородных тел) к стали, винипласту, стеклу, фарфору, дереву, карболиту и пластмассе. Но его адгезия к алюминию и оцинкованному железу в два раза ниже, чем к стали. Учитывая возможность коррозии стали при определенных атмосферных условиях, рекомендуется применять при склеивании крепежные детали из пластмасс (за исключением полиэтиленовых). Норма расхода клея БМК-5К составляет около 100 г на 100 креплений.
Приклеивание по сравнению с другими способами крепления проводов и установочных изделий повышает производительность труда в 2 – 3 раза.
При работе с клеем БМК-5К необходимо соблюдать некоторые нормы охраны труда и правила пожарной безопасности. Рекомендуется работать в тонких эластичных резиновых перчатках, а при приклеивании деталей к вертикальным плоскостям или потолку надевать защитные очки. Разбавлять клей надо также в защитных очках, соблюдая осторожность. Прием ацетона или клея БМК-5К внутрь даже в малых количествах может привести к отравлению и слепоте. При попадании клея на кожу его удаляют тампоном, смоченным в ацетоне, и промывают кожу горячей водой с мылом. Протирать руки ацетоном и мыть горячей водой с мылом нужно также каждый раз после окончания работ.
Не допускается работа с клеем вблизи открытого огня и нагревательных приборов. Запрещается принимать пищу и курить в помещениях, где приготовляют клей или работают с ним. Эти помещения должны иметь вентиляцию и систематически проветриваться. Просеивание наполнителей можно производить только в респираторах.
В настоящее время для данных целей можно использовать клей серии «Момент–Монтаж» [19] или клеи под названием «Жидкие гвозди» отечественных и зарубежных фирм изготовителей. Данная серия клеев предназначена для быстрого и надежного крепления тяжелых конструкций, требующих высокой прочности и долговечности. Применяется при установке наружной обшивки, сайдинга, кровли, черных полов, каменной облицовки, стеллажей, столешниц и других тяжелых деталей из дерева, гипсокартона, металла, ДСП, фанеры, камня, резины, стекловолокна и т.д.
Данная серии клеев обладает повышенной прочностью приклеивания, склеивает в различных сочетаниях большинство строительных материалов, открытое время (для позиционирования склеиваемых деталей) 15 минут, диапазон рабочих температур от -17°С до +40°С, стойки к погодным условиям, температура эксплуатации клеевого соединения от -40°С до +70°С, первоначальная сила схватывания 55 кг/см2, конечная сила схватывания 70 кг/см2.
Состав клея серии «Момент–Монтаж»: синтетический каучук, смолы, наполнители, смесь алифатических углеводородов, толуол.
Указания по применению: склеиваемые поверхности должны быть сухими, очищенными от грязи и масел, сильно прижать склеиваемые поверхности друг к другу, наибольшая прочность склеивания достигается через 24 часа, следы свежего клея можно удалить бензином или ацетоном.
Меры предосторожности: Горюч! Работы проводить вдали от открытых источников огня, в хорошо проветриваемом помещении. Избегать контакта с кожей и глазами, использовать перчатки. Пары не вдыхать. При попадании на кожу или в глаза промыть водой и при необходимости обратиться к врачу. Предохранять от воздействия солнечных лучей и не допускать нагрева свыше 50°С. Хранить вдали от источников тепла в прохладном, хорошо проветриваемом помещении при температуре от -20 оС до + 50 оС.
|